Introduction:
Paving units such as flags, kerbs and block pavers come in a variety of textures. While many of these textures are created for aesthetic purposes, some are implemented for reasons of safety.
Texturing can also occur with monolithic surfaces .
Prime examples of texturing for safety could include dimpling of a monolithic concrete or asphalt surface to improve traction (as is done on sone concrete highways in Britain and Ireland), or, on a more local scale, the use of barface or hobnail segmental paving on access ramps.


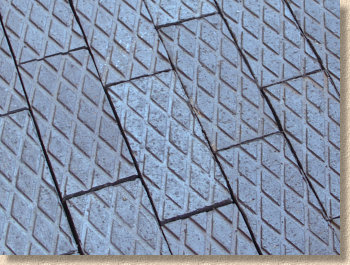

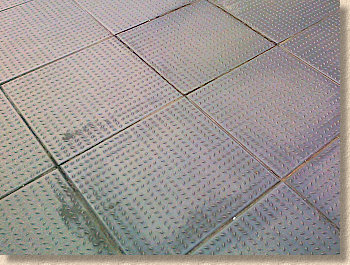
Some textures occur naturally , especially with stone products, while some textures are " standard ", that is, they are produced when the unit is manufactured, and others come about via secondary processing . Generally speaking, units that have undergone secondary processing are more expensive than 'standard' products.
Obviously, the type of paving unit has a direct bearing on the possible textures and finishes, but as technology advances, it is becoming easier and easier to apply almost any texture/finish to any product.
For example, riven stone flags have a distinctive natural texture that has been mimicked by some concrete flags with varying degrees of success for many, many years. As the manufacturing processes have evolved, so has the level of mimickry, almost to the extent where it can be difficult for the average person to differentiate between natural and reproduction units. And now the reproduction riven surface is not solely confined to natural stone and concrete copies, but some clay pavers and porcelain pavings are now being produced with a so-called 'riven effect' finish.
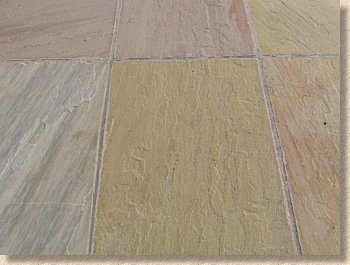
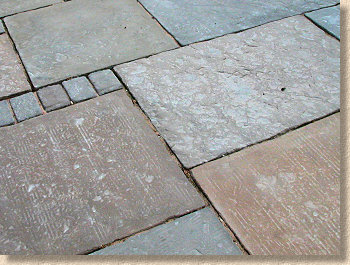
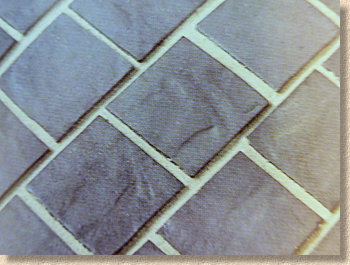
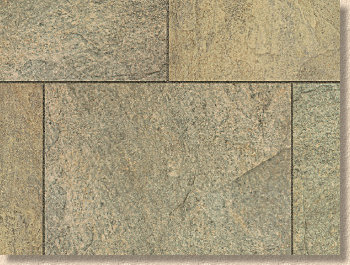
Natural textures:
This class of texture is found most commonly on quarried products, although, as already mentioned, it is sometimes imitated by manufactured pavings such as clay, porcelain and concrete.
Most stone is quarried as large blocks that are then further worked to create of flags, kerbs, setts, etc. The stone may be split along bedding or lamination planes to achieve the classic "riven" appearance; it might be cropped, a common option for smaller units such as setts; or it may be sawn.

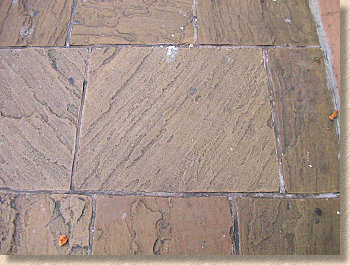
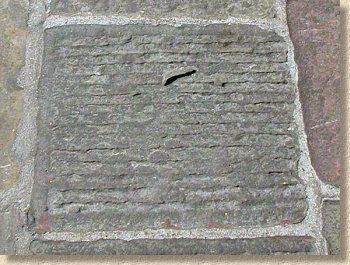

Once the stone has been quarried and reduced to its basic form (ie, a flag, kerb or sett) it can be subjected to secondary processing to create wide range of finishes, some of which are shown on the Stone Paving page.
Standard textures:
This class of texture is found in manufactured materials that are not put through secondary processing. The texture arises from a combination of the raw material characteristics and the manufacturing process itself. The two most popular materials used for paving unit manufacture are concrete and clay, and these are considered in the following sub-sections.
Concrete
Concrete is, by far, the most common material used for paving manufacture in Britain and Ireland, and it is the nature of the concrete and the form of the moulds used in the manufacturing process are the two controlling factors.
A massive amount of time and effort has been spent developing specific concretes to achieve the best possible results for each type of manufacturing process, and the typical concrete used in the manufacture of, say, pressed flags or block pavers, is quite distinct from the concrete churned out of the back of a ready-mix wagon when pouring a foundation. The cement content, the proportions of coarse and fine aggregates , and the maximum size of the coarse aggregate will all have a direct bearing on the finished texture, and so Concrete Technologists make entire careers out of tweaking the various recipes for concrete.
For most paving, a close or 'tight' finish to the concrete is desirable, although for some specialist pavers, such as the permeable products that are being developed in answer to the SUDS requirements, an open texture is required.
The second controlling factor is the mould. The plastic concrete is 'shaped' by the mould, and so the finished unit mirrors the surface characteristics created in the mould. These come in a bewildering array of forms, but the two main types are the wet-cast moulds and the hydraulic press moulds. Wet-cast Moulds are often polyurethane or ABS plastic formers that provide shape for a measure of wet concrete that is vibrated to expel air pockets and create a smooth surface, while Press Moulds are much more robust affairs, manufactured in steel to withstand the force of the hydraulic press and vibration that is used to compact and squeeze the semi-dry concrete into shape.
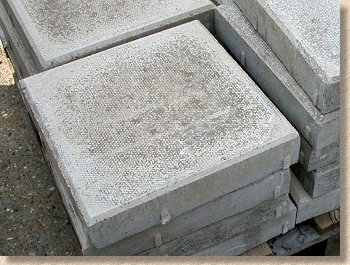
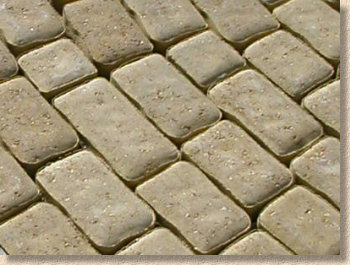
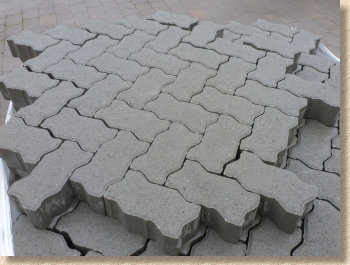

The mould is responsible for creating the overall shape and size if the paving units, and also for creating the fine detail which might be an imitation riven finish for a wet-cast flagstone or a pimple finish for BS pressed kerbs. Some units such as block pavers have little or no surface detail, other than a chamfered arris on the top face and spacer lugs on the sides, while other products, such as Bar-face or tactile flags, require finely-tooled moulds with intricate detailing.
Clay:
The other popular material for manufacturing paving units is clay, and many of the comments made about concrete and moulds apply equally to manufacturing using clay. The nature and consistency of the clay, and the qualities of the moulds are key controlling factors in determining texture. Most standard clay pavers are wirecut, which produces a characteristic, natural-looking texture, although more decorative units are often press moulded, which tends to create a smooth, ceramic-like finish.


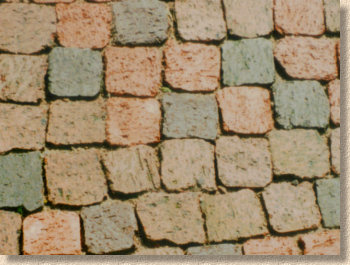
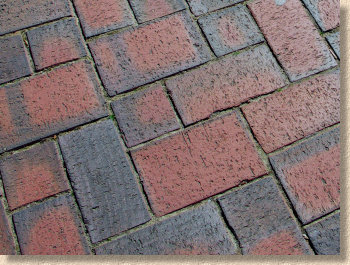
Secondary Processes:
Secondary Processes is the term used to describe texturing techniques that are applied to paving products following initial manufacture. These processes include popular textures such as 'Tumbled', Shot Blasted and Polished, amongst others.
As this subject is quite involved and requires the use of a lot of images, it has been given a separate page, which can be accessed by clicking here .
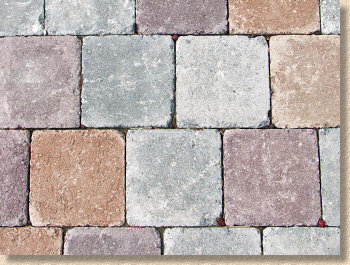
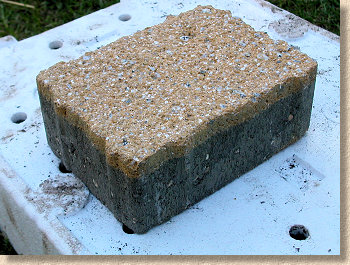
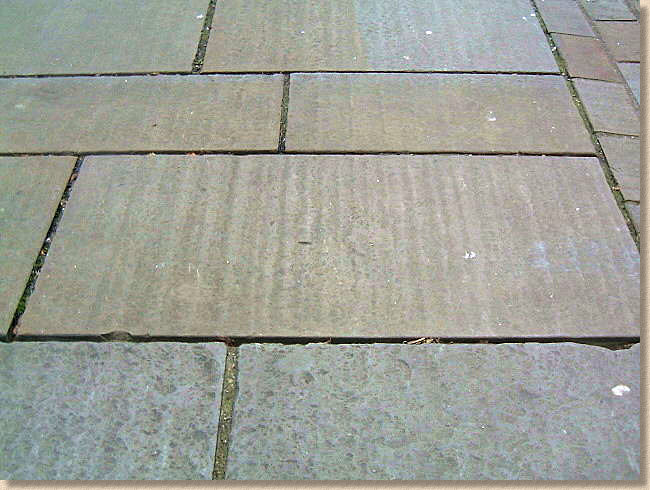