Introduction:
The publication of part 12 of the ever-growing set of British Standards devoted to modular/elemental/segmental paving (BS 7533) has been a significant fillip to the proprietary mortar industry as it has spurred specifiers and engineers to move away from traditional site-batched mortars for bedding and jointing. Most manufacturers provide both a bedding and a jointing mortar, and it surely comes as no surprise to learn that each manufacturer swears blind that their bedding blend, in conjunction with their jointing jollop is the answer to all your prayers, and that it's less than ideal to mix a bedding product from one manufacturer with a jointing material from another.
BS7533:12 ~ Parameters | |
Compressive strength | > 40 N/mm² |
Adhesive strength | > 1.5 N/mm² |
Flexural strength | > 6 N/mm² |
Modulus of elasticity |
20,000 ± 4,000 N/mm² |
Density | > 2,000 kg/m³ |
Shrinkage | < 0.15% |
It is for the specifier or engineer to decide which particular product is most suitable for their particular project. No one product range is the answer to every project, so what follows is a generalised overview of the more popular products.
The jointing material is delivered in pre-weighed packages, and it is intended that each package is mixed with a stated quantity of clean water. Mixing half-a-bag to effect a patch repair or to joint a smaller area is frowned upon, but, if both the product and the pro-rata volume of clean water are carefully controlled and checked, there should be no problem. However, it is NOT a good idea to save "for another day" a pack that has been opened. Any packs opened should be used that day or they should be binned as the cement will be compromised.
Tools:
- Mixer (rotary/cement)
- Soft brush
- Stiff brush
- Squeegee
- Optional: Vibratory rubber roller
- Optional: Belt cleaner
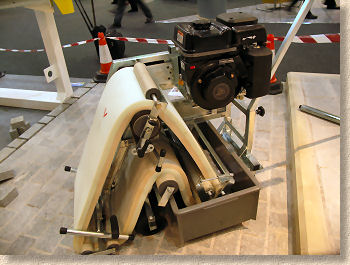
Technique:
The pavement should be inspected prior to jointing. Joints should be cleaned of any detritus, vulnerable surfaces should be protected with polythene sheets or similar, the lifting eyes and the gaps between frame and cover on utility fittings should be sealed or covered to prevent them being inadvertently mortared, and then the area of pavement to be jointed should be doused with clean water to ensure the whole surface is thoroughly wet prior to placing the slurry. Placing mixed jointing material onto a dry surface is likely to result in staining that may be difficult, if not impossible, to remove.
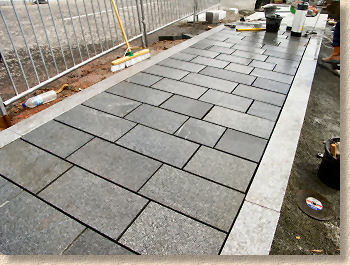
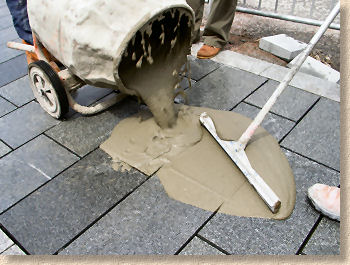
The jointing material and clean water are best mixed in a rotary (cement) mixer following the manufacturer's instructions to the letter. This usually involves adding half the stated quantity of clean water to the rotating mixer, then adding the dry powder product, and finally adding the remaining volume of water. Putting powder into the mixer first can result in 'balling' of the jointing material and produce an unevenly mixed 'lumpy custard' slurry.
As soon as a batch is mixed, it is emptied out onto the pre-wetted pavement surface and chased into the open joints using a soft brush or a squeegee. The grout is spread over the entire surface and not simply chased along the joints. This ensures the whole surface has been subjected to the same treatment and should therefore avoid any difference in finished appearance between grouted and non-grouted areas. As the slurry settles into the empty joints, joints are repeatedly "topped-up" by passing over them with more of the slurry until no further settlement occurs.
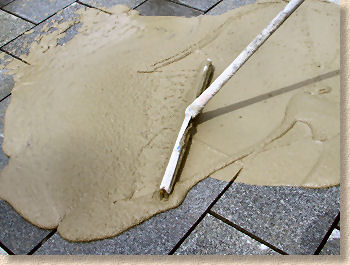
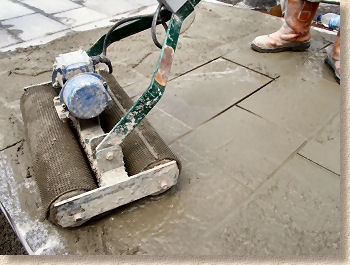
One jointing system supplied by Acosim UK , although originally developed in Switzerland, uses a small vibrating roller to gently rattle the surface and drive the mortar deep into the joint and into the porous bedding material that is recommended be used with this particular system. This is claimed to result in an inverted T-bar of jointing mortar that holds firm the paving elements in all three dimensions.
Alternative proprietary grouts are available from other manufacturers, including Ultracem from Instarmac and Tufftop from SteinTec , both of which are excellent products.
It may be necessary to lightly spray or mist the surface during jointing to prevent parching or drying of the slurry before it can be removed. The trick is to keep the jointing material wet at all times until it can be cleaned off.
Once the joints are filled and there is no sign of settlement, as much as possible of the excess material is swept clear of the surface prior to final cleaning. On smoother paved surfaces (sawn or flat-cleaved stone), a squeegee can be very effective at removing almost all of the excess, but rougher surfaces (cropped setts/cubes or riven flagstones) are best cleaned using a series of brushes.

Again, it is vitally important that the surface is kept wet throughout this initial clean: a fine spray or mist is best for this, as it is much less likely to disturb the material within the filled joints than a hose or power washer played over the surface by a bored witless labourer mindlessly scrawling the name of his footy team with the water jet. Any residue or excess taken off the pavement should be disposed of carefully, making sure it cannot contaminate the paving, or any other surface.
Cleaning:
Most proprietary jointing mortars have a relatively fast initial set, and this allows the pavement to be washed clean shortly after jointing is complete. Timing is the essence of successful cleaning. Sufficient time must be allowed to afford the mortar a chance to fully settle into the joints and begin to harden but if left too long, it can start to bond to the surface, making a thorough clean that much more difficult. Ambient temperature and humidity will affect the timing (faster when it's warm/dry; slower when chilly/damp) as does the presence of direct sunlight (slower in the shade; faster in the sun). The mortar remains cleanable for longer in the cooler months, but it can be a real race against the clock on hot days, when, it can be argued, jointing is best left until the late afternoon or early evening for best results. As with so many skills in the paving trade, timing the clean is something that is learned with practice, and not something that can be precisely defined in text.
Over the years, many different methods of slurry cleaning have been tried, with varying degrees of failure. Hosing down, mist-and-sweep, sawdust, clean sand, brush-to-dry, etc. None of them can reliably produce a clean surface, and many of them involve more time and effort than did the actual jointing or laying. Of all the manual cleaning techniques, simple hosing down is probably the most effective.
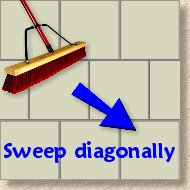
The slurry residue can be washed off using copious amounts of clean water, aided by a soft brush being swept at an angle to the jointing. Never brush along the joints: this can remove jointing material. Instead sweep across, as this is much less likely to disturb the joint. Most contractors will sweep diagonally to the jointing so that the whole pavement can be cleaned in one movement without compromising either transverse or longitudinal joints.
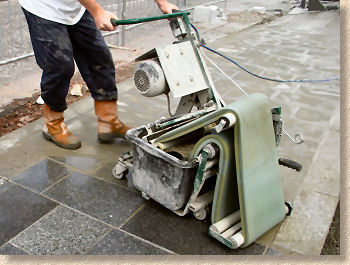
Belt cleaning machines are becoming increasingly popular for final cleaning. In essence, a continuous belt of resilient fabric is passed first through a water bath to wet it, then it is drawn over the freshly-jointed surface, wiping away some of the excess mortar, before being passed through a scraper and/or a water bath to remove the collected mortar, clean the belt and re-wet the fabric in advance of a further pass.
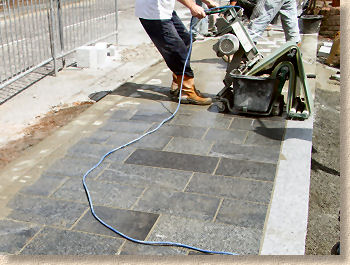
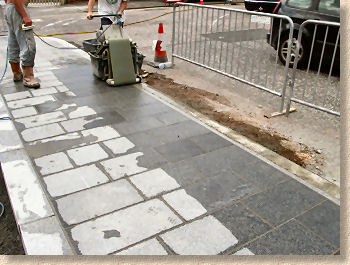
They reduce the volume of water required to clean a jointed pavement, which can be highly significant on some projects such as town centre schemes, they collect the residue rather than allowing it wash down the street into the sewer system, and they can reduce the amount of labour required to achieve a high standard of cleaning. However, while a good quality, well-maintained belt cleaner guided by a skilled and experienced operative can remove 90% or more of the slurry from the surface of a pavement, there are always places that the machine cannot reach: tight-up against a wall or other vertical projection; internal corners; rebated ironwork covers, etc., and so it is always necessary to complete the cleaning by getting down on hands and knees with a sponge and a bucket of clean water.
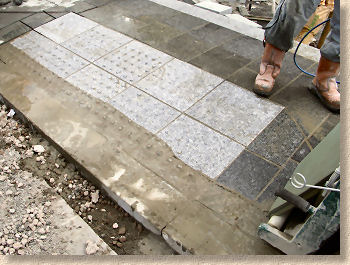
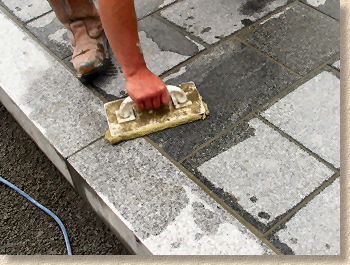
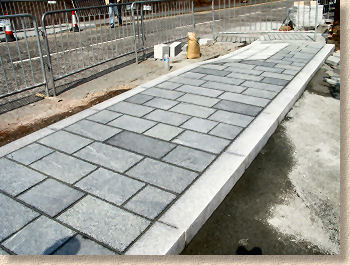
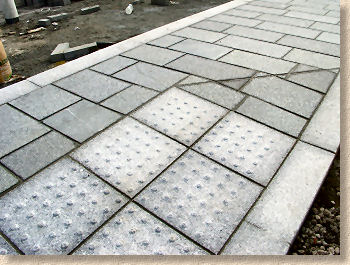
It's often possible to identify the better contractors simply from the cleanliness of their completed paving. The good contractors will ensure their paving is spotless, with all residue removed and utility covers lifted and re-fitted to ensure they are free. Less diligent workers often overlook these points.
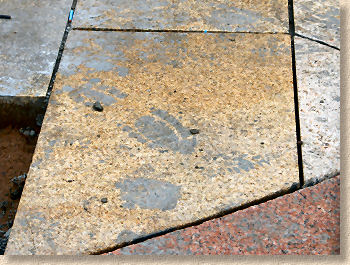
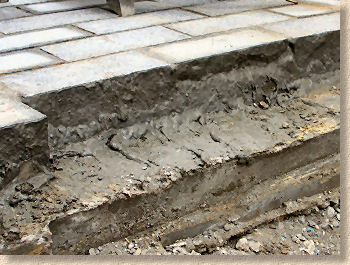
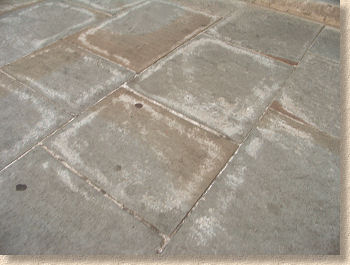
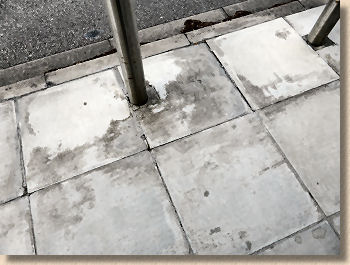
Examples
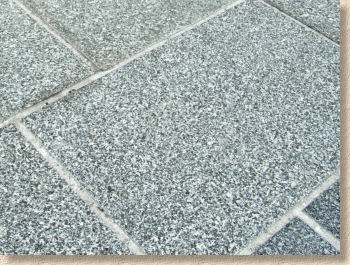
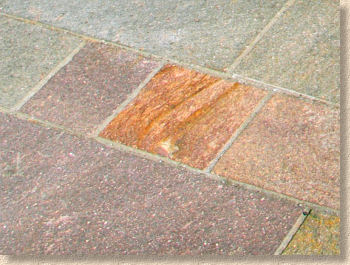
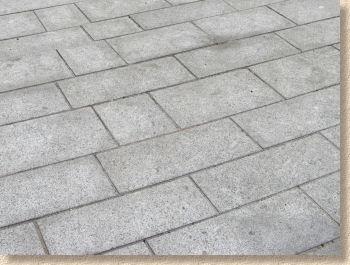
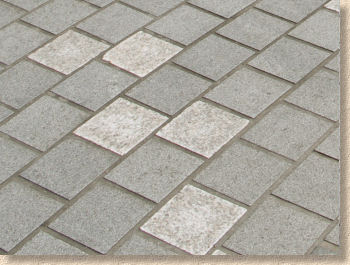
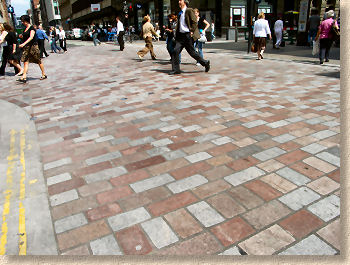
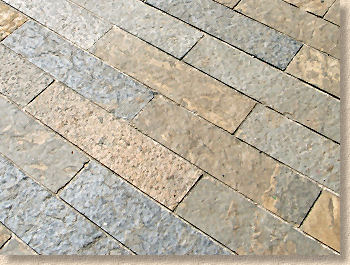
Comments:
Slurry or grout jointing followed by washing or belt-cleaning is developing to be the most popular method used for commercial and specification projects. When undertaken with a degree of diligence and care, it is highly effective and can be undertaken by semi-skilled labour. However, in the wrong hands, it can easily degenerate into an unmitigated disaster. In particular, care and attention to the timing and thoroughness of the cleaning effort is key to a successful jointing procedure.
Although use in the residential market is limited at this moment in time, as the technique becomes better understood and more widely practised on commercial projects, it is likely to find further opportunities on these smaller scale projects. It can only be a matter of time before the belt cleaner, like the block splitter and plate compactor, become a standard tool in the pavior's armoury.
Thanks to Grant Wilson at Acosim UK for allowing an installation using the Samco 88 mortar to be photographed and videoed for this project.
Other pointing and jointing pages...
- Introduction
- Terms & definitions
- Pointing Styles
- Spacers for Paving
- Cement Mortars
- - Hand Pointing
- - Pointing Riven Flagstones Using Coloured Mortar: A Case Study
- - Wet Grouting
- - Dry Grouting
- - Slurry Grouting
- - Steintec Tufftop Slurry Grouting
- - Gun Grouting
- - Poured Grouting
- Resin Mortars
- - Polymerics
- - GftK Polymerics: A Product Study - VDW 840+
- - Romex Polymeric Mortars: A Product Study
- - Jointex Polymeric Mortar: A Product Study
- - Slurries
- - GftK Slurry Mortars: A Product Study - VDW 800 Permeable
- - GftK Slurry Mortars: A Product Study - VDW 850
- Re-jointing paving
- Pitch Jointing
- Loose Fill Jointing
- - Stabilisation
- Alternative Jointing Materials