Introduction:
Vast quantities of rock are quarried for road-building stone, for cement production and for surfacing materials ranging from York Stone Flags to Pattern Imprinted Concretes and asphalts, river channels and estuaries are dredged for sands and gravels, clays are extracted for hoggin and for pipe and brick production.
However, the industry has, like the rest of the world, had to face up to its environmental responsibilities, and so there is now a conscious effort to recycle and re-use aggregates and other materials if at all possible. Old concrete is crushed, graded and sold as selected fill; bituminous roads are planed down, heated up, re-mixed and relaid in one operation and the demand for reclaimed stone flags, setts and cobbles seems greater than ever. We probably won't ever see an end to quarrying, after all, humankind has been hacking and hewing away at the hills for thousands of years, but we can make best use of the resources we have, and ensure that we minimise the impact our modern society imposes on our natural environment.
This page provides basic information on the aggregates most commonly used in the paving industry.
Ash - Cinders
Up until the mid-late 1970s, ash (aka 'clinker' or 'cinders') was routinely used as a bedding material for all sorts of pavings, but the demise of the coal-fired power stations, along with the concurrent reduction in other coal-powered industries such as textiles (up here in the north), steel-making, etc., saw the volume of available ash reduced and it has now been almost completely replaced by sands and grits. Being considerably less dense than sand or other quarry products, ash was a bedding material much-admired by the laying gangs, as it is easy to cart and to spread, and compacted well.
It also had a couple of lesser-known uses; it was mixed with cement to make 'ashcrete' a lightweight cement-bound fill material suitable for non-load-bearing applications, and there were also pre-cast flags/slabs that known as 'cinder-backs' or 'ash-backs' that had an upper face of a dense, hard-wearing concrete atop a base of 'ashcrete'. As a boy in the 1960s, I recall seeing these 'cinder-backs' being manufactured at a small works in St Helens Junction, Lancashire, during a visit to the factory with my father.
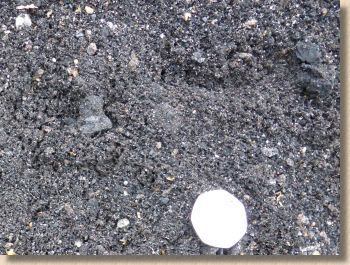
Nowadays, Pulverised Fly Ash (PFA) is a by-product of the modern power stations. The coal is crushed to a miniscule size, usually less than 1mm before being injected into the furnace and burnt . The resulting waste ash is used as a fill material and PFAs with a high silicon content can be used in specialist concretes as a partial replacement for cement.
Asphalt
A black hydrocarbon that occurs naturally and can be manufactured as part of the oil distillation process. Chemically quite similar to bitumen. Asphalt is used in 2 main ways - as mastic asphalt for waterproofing, particularly on bridge decks, and as rolled asphalt (aka Hot Rolled Asphalt or HRA) for road and pavement surfacing.
Asphalt is also used as a generic term in Europe and North America to include all asphalts and bitumen coated materials.
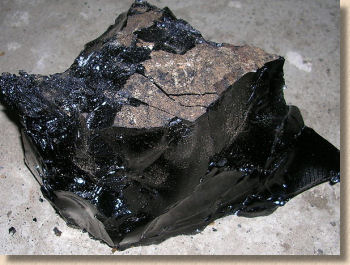

See also....
- Bitmac (below)
- Tarmacadam Page
Ballast
As with a lot of terms used for aggregates, this one has several meanings. In some parts of the country, 'all-in ballast' refers to a mixture of gravel and/or small stone (<60mm) with sand, often used to make concrete. Elsewhere, it can refer to the coarse granular stone (around 40-50mm in size) used to support railway lines or as a general 'fill' material of crushed rock, slag or gravel.
The so-called "All-in Ballast" commonly provided in DIY sheds or Builders' Merchants is whatever they want it to be at any given time. It can be anywhere from 100% fine agg (sand) to 100% coarse agg (gravel) with no control over the quality or grain shape. It is, literally, the sweepings-up from the quarry power screener, the stuff that didn't get sorted.
As such it should never be used for any critical concrete, such as floor or base slabs. It's OK for, say, fixing fence posts but you should bear in mind that there are good reasons why the industry specifies separate quantities for the fine and coarse agg when mixing a concrete .
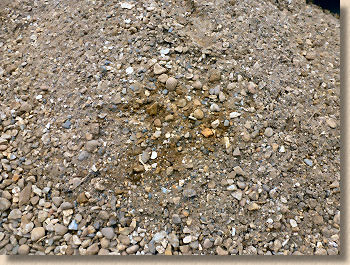
Bitumen/Bituminous Macadam
Bitumen is a sticky black mixture of hydrocarbons occurring naturally or produced as part of the crude oil distillation process. It is soluble in carbon disulphide.
It is widely used in the paving industry to coat aggregates to form Tar Macadam (Tarmac) or Bituminous Macadam (Bitmac). A sizable section of the construction industry is devoted solely to the chemistry, production and usage of bitumen products and as such, it is impossible to give comprehensive coverage of the subject on this site, although a general overview is given on the Tarmacadam page.
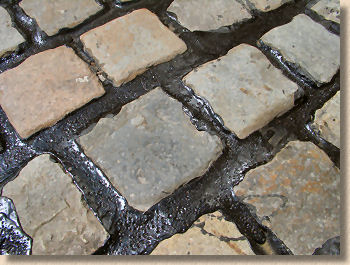
In its raw form, bitumen, or pitch as it is sometimes refererred to, was once the preferred joint sealant for sett paving, although this role has diminished as the area of sett work undertaken each year has reduced and as high-strength mortars have become more readily available.

See also....
- Asphalt (above)
- Tarmacadam Page
- Sett Paving
Cement
Cement is a powder manufactured from limestone that is mixed with other aggregates and clays, notably sands, gravels and stone, to produce mortars and concretes. The vast majority of cement used in Britain and Ireland is Portland Cement, sometimes referred to as Ordinary Portland cement or OPC, although there are also specialist cements, such as Sulphate-Resistant Cement (SRC) which is often used for sub-surface works, and High-Alumina Cement (HAC).
It is generally sold in 50kg and 25Kg paper sacks, although the big commercial users, such as concrete batch plants and pre-cast manufacturers will often take delivery via powder tankers.
Cement is NOT the same as mortar or concrete, but is a component thereof. A pet bugbear of mine is the incorrect use of the word by the general public who use the term as a catch-all word for mortar, concrete and cement powder.
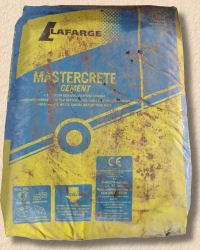

See also....
- Concrete (below)
- Mortars and Concretes Page
- Concrete Mixes
Clay
Clay is primarily used as a source material for brick-making. Selected clays are extracted and shaped into bricks or pavers , either by hand or by machine, before being baked at high temperatures in a kiln. Different clays give different colours of brick, and will also determine other properties, such as hardness, frost-resistance, water-absorption etc.
Second to brick-making, clay is used in the manufacture of drainage pipes and fittings where again, the clay is prepared and worked to shape or extruded into pipes before being fired in a kiln.
Clay is also used a general fill material on earthworks projects and specialist clays, such as Bentonite, used in the drilling industry, may have commercial applications outside the construction industry.
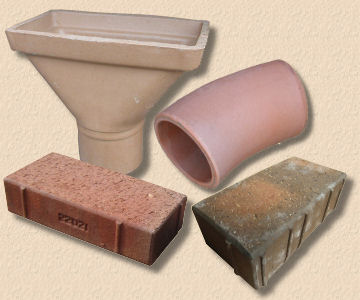

See also....
Coarse Aggregate
This has become a catch-all term for any aggregate which has particles of around 4mm or greater. It mostly tends to be referred to when specifying concretes which requires certain proportions of fine aggregate and coarse aggregate.
So, it would include gravel, whether it is crushed or rounded, as well as all sorts of other crushed and naturally occurring aggregates. It can also include secondary aggregates such as crushed brick, slag, slate waste or recycled concrete.
The full definition for a coarse aggregate is set out in BS EN 12620:2013 Aggregates for concrete.
A typical coarse aggregate might be specified as....
G c 85/20
....and all this gibberish is explained in the section on Sand below.
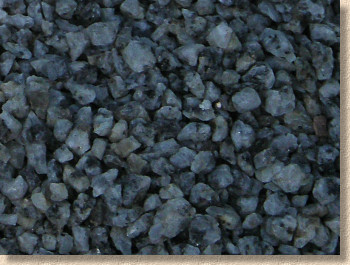
Concrete
Concrete is a mixture of sand , coarse aggregate or gravel and cement that sets hard within a few hours of being mixed with water. The proportions of the fine aggregate (sand), coarse aggregate (gravel), cement and water are varied to give concretes of different strengths and workabilities . The amount of water used to mix a given volume of concrete is determined by the Water:Cement ratio (W/C ratio) which works on the principle that a a smaller quantity of water (lower W/C ratio) results in a stronger concrete (assuming proper compaction).
Concrete is graded according to its characteristic strength after 28 days of curing, with a Class 7.5 mix being a relatively weak concrete for fill purposes or for bedding of kerbs, while a C40 mix is a relatively strong mix suitable for cast in-situ work and load-bearing applications. Information from BS EN 206 giving mix parameters for various grades of concrete is given on a separate page .
Most concrete is delivered by special wagons from 'Batching Plants' which mass produce concrete of a guaranteed quality on demand. Most of the larger, national companies belong to the Quality Scheme for Ready Mixed Concrete (QSRMC) to guarantee their product meets or exceeds the requirements of the specifications. On larger projects, batching plants may be especially set up solely to provide concrete for that project.
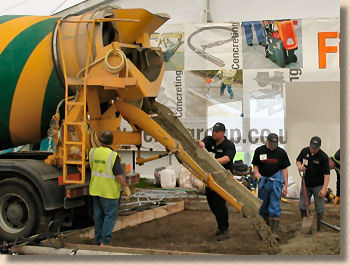
For smaller quantities, concrete may be mixed on site in small mechanical mixers that can churn out 0.25-1.0 m³ at a time, or for very small quantities, it may be mixed by hand.

DTp1
This is the most commonly recommended material for constructing a sub-base. The full title is Granular sub-base material to Type 1 of the Department of Transport Specification for Highway Works (Clause 803). It is usually a crushed rock, typically limestone, granite or gritstone, although it may be slag or some other inert hard material.
It is stubbornly and inexplicably often referred to as MOT even though the MOT (Ministry of Transport) disappeared in the 1970s!
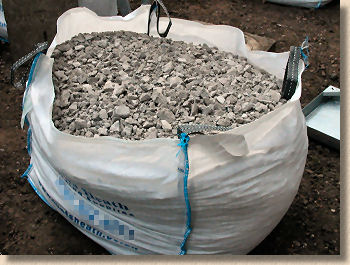

See also....
Glass (recycled)
Large quantities of glass waste or cullet is produced each year in Britain and Ireland and there have been several initiatives to develop uses for recycled glass as an aggregate for the construction industry in the past decade. With the greater focus on recycling within the EU since the beginning of the new millennium, we expect the markets and opportunities for recycled glass to expand in the coming years.
Some of the more successful current uses for recycled glass include...
- Tumbled glass as a decorative aggregate for surface dressing and/or mulches
- As a laying course material for flexible block paving , when crushed/tumbled to sand grain sized particles
- As a decorative coarse aggregate in concrete flags , kerbs and block pavers
- As fine aggregate in concrete blocks
- As a filler and aggregate in asphaltic base/binder course products such as "Glasphalt"
- As a filter medium in specialist drainage schemes
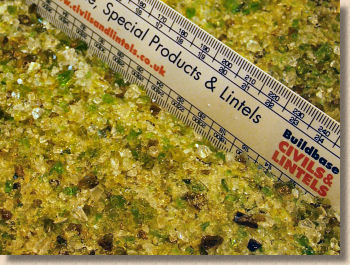
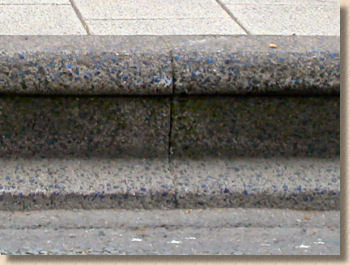
Gravel
A granular material which can be of almost any rock type. Gravels are usually sized between 60mm and 2mm and may be rounded, when from a marine or fluvial source, or angular when quarried and crushed. Gravels are sold in size ranges, e.g. 20-5mm or closely graded to a specific size, such as 10mm.
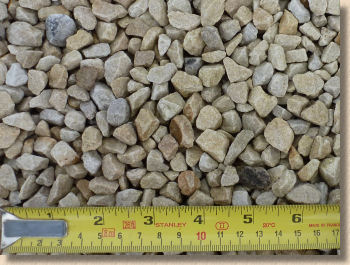
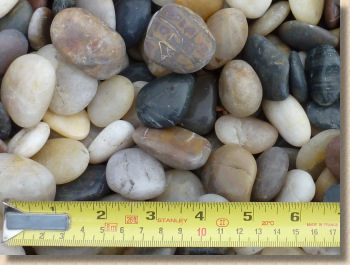
Gravel has many uses in the construction industry, including pipe-bedding , coarse aggregate for concrete and as a resin- or bitumen-bound surface dressing (tar-and-chip).
Grit
Another granular material that can be thought of as a transition stage between a coarse sand and small pebbles. Generally 2-6mm in size, grit traditionally had limited uses in the construction industry on its own, other than as a surface dressing. However, over recent years with the development in block paving specifications, it has become a viable alternative bedding and jointing material for permeable paving and other forms of elemental paving used in areas of high water ingress.
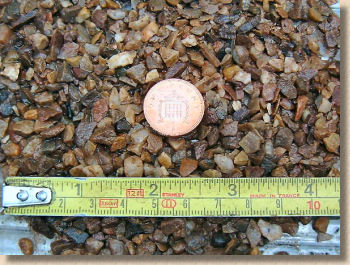
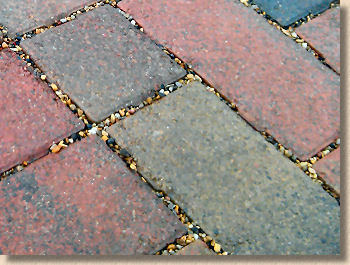
Hardcore
A term that has unfortunately been usurped by the porn industry and which provides a constant source of amusement to me when I see the web logs for just how many saddoes have used their one free hand to surf over to this site in search of hardcore, only to find a pile of old bricks and broken concrete.
Generally, hardcore is any hard, crushed inert material that can be used as a fill, although it is generally thought of as demolition waste and rubble. In these environmentally-friendly times when we have a progressive tax regime imposed on the dumping of waste materials, more and more 'hardcore' is being crushed and processed to form suitable fill material or even sub-base material for all sorts of construction projects.
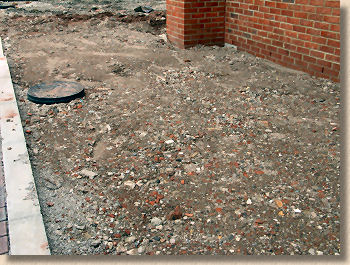
Increasingly, crushed concrete is being used as a good quality hardcore that is even capable of acheiving the hallowed status of DTp1 . However, there is an awful lot of utter crap out there. Little better than skip-fill. Truly poor quality crushed demolition waste with all sorts of undesitrables included, such as bits of timber, weeds and degraded bitmac (see road planings below)
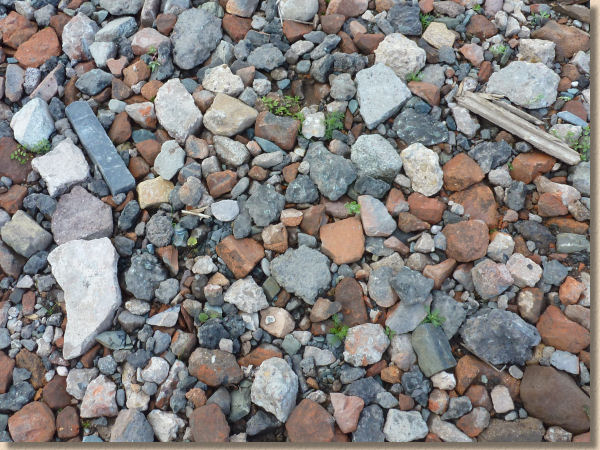
Hoggin
A well-graded gravel mixed with sand and natural clay as a binder and used as a surfacing for low-speed driveways and footpaths. Common in the aggregate-poor south-east of England, but rarely seen any further north than Birmingham.
At best, it's a convenient near self-binding gravel; at it's worst, it's nasty, claggy crap.
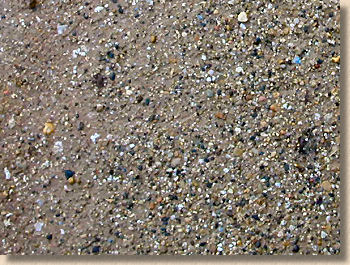

See also....
MOT 1
In Britain, they got rid of the old Ministry of Transport (MoT) in 1972 when it became The Department of Transport, abbreviate to the DTp, and what was MoT Type 1 granular sub-base material became DTp Type 1 granular sub-base material, which was, by some cosmic coincidence, exactly the same!
However, seeing as that is a mere 40-odd years ago, the building trade hasn't really had enough time to get accustomed to this radical change in name and so we have allegedly 'professional' contractors still referring to the aggregate as "MoT 1".
Since then, the actual specification for a Type 1 material has been tweaked, but it is essentially the same, although it can (nowadays) include some crushed clean, hard brick and crushed recycled concrete.
Planings and Asphalt Arisings
When a bituminous or asphaltic road surface is renewed, the old surface is often removed by a beast of a machine known as a Cold Milling Machine, or, more familiarly, a Planer, which mills and reduces the existing surface to chunks, that may be anywhere from 150mm in size right down to dust. In some cases, these planings, as they are called, may be recycled by re-heating an mixing with a fresh binder to create a new bituminous or asphalt-bound surfacing material, but quite often they are used as a poor quality fill, often ending-up on farm tracks and the like.
Because the planer has limited control over the size of the planings generated, the resulting material is too hit-and-miss to be regarded as a useful sub-base material. Post-planing screening to remove dust and larger chunks can be used to generate a more even-sized material, but the additional processing bumps up the cost.
Planings are not considered to be a suitable fill or sub-base material for most construction projects because bitumen is a perishable product and as such, will degrade over time, which could lead to problems of settlement of worse should they be used in any load-bearing capacity.
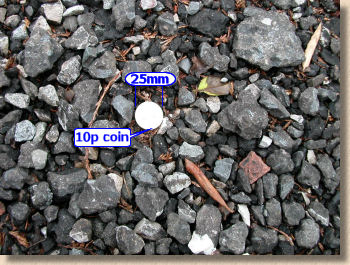
However, asphalt arisings, which do NOT include tar or bitumen based materials (so that means most planings) are regarded as a suitable sub-base material, designated as Type 4 in the Specification for Highway Works (Clause 807), and so should be considered separately from the (literally) run-of-the-mill planings from typical highways.
Sand
There seems to be more confusion regarding the different types of sand than any of the other aggregates. Sand is composed of grains of rock, in the size range 0.06mm to 4.0mm, mostly quartz, (aka silica or SiO 2 ) although there are often other minerals mixed in, especially clays and iron, which gives some sands their distinctive reddish colouring.
They occur as natural drift deposits, especially in marine and/or fluvial environments, although some of the coarser grit sands are produced as a by-product of quarrying and rock-crushing.
A uniform sand consist of grains of mainly one size range, be it coarse[C], medium[M] or fine[F], whereas a graded sand contains a mixture of grain sizes. This runs counter to everything I learned as a student of geology, where a graded sand is one where the grains are predominantly of one size, ie, what civil engineers call a uniform sand.
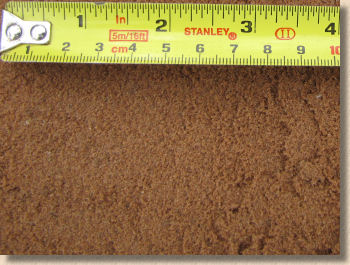
Red sands are more common in N and W Britain
For general on-site construction purposes of the paving persuasion, there are two main working categories of sand, namely building sand (aka soft sand) which is primarily used in the preparation of mortars, and grit sand (aka sharp sand), which is used as a bedding material for paving. Naturally there are intermediate sands and applications thereof, such as jointing sand, but these are the two most regularly encountered categories.
Building Sand tends to be a finer sand, often with a fines content of 10% or more often known as a 'Soft' sand.
Meanwhile a Grit Sand will have a low clay content and a greater proportion of larger grain sizes and may ne known as a 'Sharp' sand
For laying course sands, the usual specification followed is that given in BS7533:Part 3 , for a Grit sand with strict control of the fines content. The same sand is used for the laying of Paving Flags/Slabs, setts and most unbound paving.
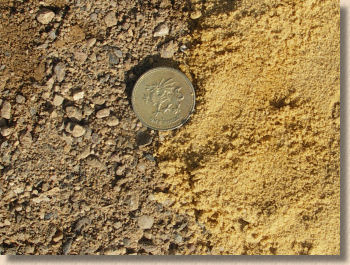
BS EN 12620:2013 - Fun with sand
You wouldn't believe how complicated the specification of sand has become over recent years. What used to be a relatively simple definition has been hijacked by the euro-bureaucrats and we now have all sorts of algebra with superscripts, subscripts and commas in place of decimal points.
Very crudely, sand for bedding used to be Coarse (C), Medium (M) or Fine (F) and that was simple enough to follow. To be fair, it was too simple and didn't allow for the subtle variations that will always occur with a natural product, but more importantly, it wasn't sufficiently prescriptive for the more technically competent building trade of the 21st century.
Then, factor in the European obsession with harmonisation and all of a sudden we are buried up to our necks in jargon and footnotes.
What follows is a highly simplified attempt at explaining how bedding sand* is now described according to the relevant British and European Standard, BS EN 12620:2013 - Aggregates for Concretes , which just happens to include laying course materials. There is far, FAR more to it all than can possibly be covered here (do you really want to know about the Flakiness Index?) but this is, hopefully, a distillation of what is directly relevant to the paving industry.
* All this applies only to sand for bedding. Sand for mortar has its own, equally baffling and equally expensive BS EN
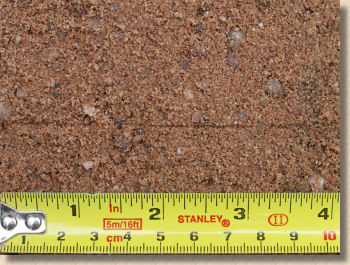
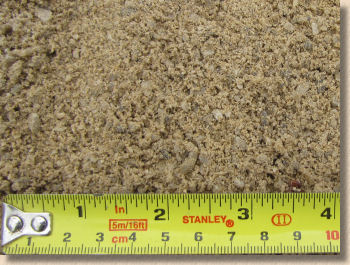
Essentially, sands now have "Categorisation" ( G ) which gives brief description of Type ( C oarse, C oarse for A sphalt, N aturally G raded or F ine) along with some numbers which are not quite as meaningless as they may first seem.
When there are TWO numbers separated by a slash, the first refers to the minimum percentage of material passing through the 'big' sieve, while the second refers to the maximum percentage passing through the 'little' sieve. When there's only one number, it is the minimum percentage of material passing through the 'big' sieve.
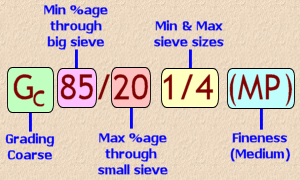
In all cases, the 'big' sieve has a 4mm mesh. Only the Coarse aggregates have a second number (small sieve) which has a 1mm mesh, but be aware that there are further grading requirements relating to the fines contents which involve a 0.5mm sieve (or 0,5mm as those danged Eurocrats would have us state).
And just when you think it sort of makes sense, they introduce a separate category, f, which is a fines value for the percentage of material passing through a 0.063mm (Oops! 0,063mm) sieve. Confused? Good – that means the Eurocrats get to keep their jobs.
So, for most paving purposes where a laying course material is required, such as block paving, the relevant British Standard (un-buggered by Eurocrats just for the moment) stipulates....
G f 85 0/4 (MP) fine aggregate
....which is decoded as follows….
G – The grading
f - is for a fine aggregate
85 – where at least 85% of the aggregate will pass through the 4mm sieve
0 – and the smallest grain size is 0mm (not really, just very, very small)
4 – while the largest grain size is 4mm
MP – and the fineness is M for Medium meaning somewhere between 30-70 Percent of the aggregate will pass through a 0.5mm sieve.
For laying course sand beneath block paving, there are further requirements on the fines content over and above the MP designation. These are explored below .
Brain aching yet? Think yourselves lucky we don't need Micro-Devals or Los Angeles Coefficients!
To check that you've been paying attention, here's the 'official' title for Jointing sand. Decode this....
G f 85 0/1 (FP)
....the big difference in this example is the (FP) bit which states the fineness. In this case, FP means F ine and in P ercentage figures, that means 55-100% of the aggregate will drop through the 0.5mm sieve.
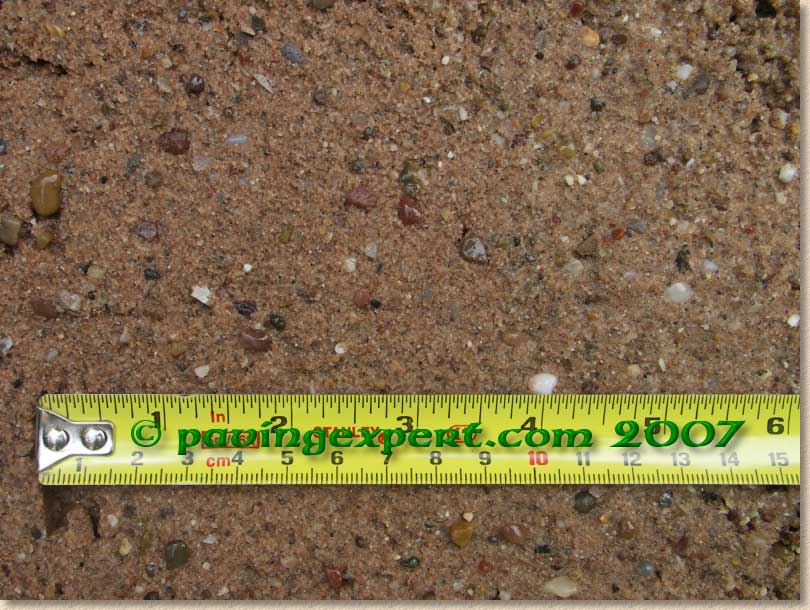
Grit sand in close-up
Fines content for laying course material
As warned about above, there is an upper limit on the fines content of laying course material and this limit varies according to the categorisation of the pavement. Essentially, the heavier the trafficking of the pavement, the lower the fines content.
Block pavements are assigned to one of these four zones (aka "categories") [was five zones pre 2009 update] based on their typical usage, and extensive research over a number of years has shown that the sands with a lower proportion of the finer particles are more reliable as bedding sands for heavy applications (zone 1 or zone 2), and that natural sands with rounded grains are less prone to settlement and fluidity than the angular, crushed-rock sands.
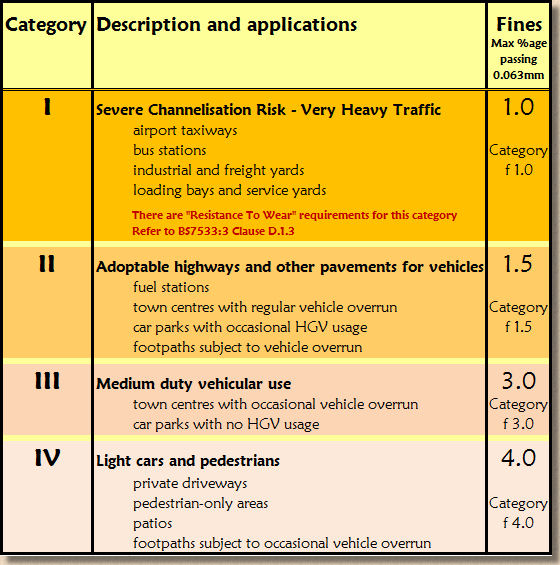
Based on a pavement's category, the maximum permissible fines content (particles of less than 0.063mm) for laying course sand is given in the table opposite.
The same table also gives the grading requirements for jointing conventional (NOT permeable) block paving. Note that the bedding sand is considerably coarser than the jointing sand.
The laying course and jointing materials for permeable block pavements ( CBPP ) are *completely* different and are considered separately elsewhere on this site.
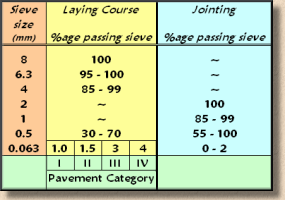
Further notes regarding sands
Rounded grains pack together tightly, giving a stable bedding layer, whereas angular grains have been found to have their 'rough edges' broken off under loading, thereby increasing the proportion of very fine particles in the sand which can be carried by percolating water, giving rise to a 'lubricating' effect which, in turn leads to separation of the sand into layers of differing grain size, possibly causing problems in heavily trafficked projects.
However, don't be daunted by all this soil mechanics micro-detail: for private driveways, patios and other low-traffic projects, a standard grit sand as sold by the local Builders' Merchants will more than likely be perfectly adequate as a bedding material. It is only for adoptable roads and high-traffic/heavy-loading applications that such in-depth consideration of the bedding layer sand is required.
Finally, two specialist sands; jointing sand, as mentioned above, is used to fill the joints of block paving and is specially selected to have a very low clay content and have grain sizes that will generate a high degree of friction, thereby giving stability and resistance to loading in a block pavement. It's also known as Kiln Dried Sand.
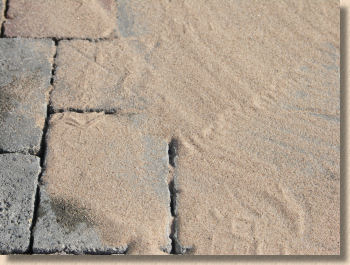
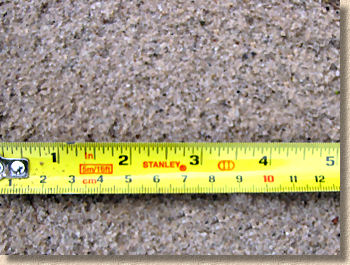
Silver sand is a sand with a very low iron content, and is much favoured in the manufacture of high-quality optical glass. Its silver (sort of) colour is a result of it being almost pure silica (SiO 2 ) and there being virtually no contamination with other minerals. It has limited uses in the construction industry, but is increasingly used as a component of the bedding mortar when laying pale or light coloured flagstones as its purity reduces the risk of discolouration.

See also....
Scalpings
Scalpings are, correctly, the off-cuts or shards created by dressing stone for building work, ie, a quarry waste. They are not as common as they once were, as we now use machinery to dress stone and the waste is re-processed into, say, a select fill, a Type 1 sub-base material , or, as mentioned above, a crushed-rock sand , but the term persists in some parts of the country.
The main use of scalpings nowadays is as a medium quality fill or sub-base material used in the construction of access paths, car parks, driveways or other light-use applications where a DTp1 is unavailable or uneconomic. As there is no hard and fast specification laid down as to what qualifies as 'scalpings', almost any quarry waste or road planings can be, and are passed off as suitable for driveway construction. For the extra couple of quid per tonne it costs for a Type 1 material, we prefer not to spoil the ship for a ha'porth of tar, as the saying goes.
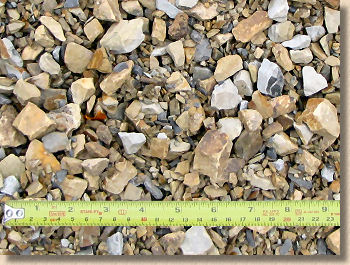

See also....
Shale
Yet another term that refers to more than one type of aggregate.
Shale is, geologically, a laminated claystone or siltstone that readily cleaves along its bedding planes.
However, in some circles, shale refers to colliery waste, which may or may not be a true shale geologically. It is often 'burnt', either by self-combustion or by industrial process, which renders it inert. It is rarely used as a sub-base material, as it tends to be far too soft, but is used as a surface dressing, especially the 'burnt red' type and is inexplicably popular for low-cost tennis courts.
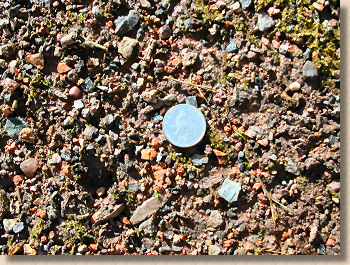

See also....
Shingle
Another non-specific term, usually referring to gravel, particularly a mixed gravel containing pebbles of various sizes, grits and sands.
In certain parts of Lower Britain, shingle seems to refer more-or-less exclusively to beach-sourced gravels of indeterminate size and rock type.
Often used in the preparation of home-batched DIY concretes.
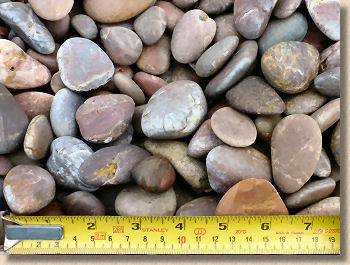

See also....
Slag
A waste product once common but, with the reduction in steel-making capacity in Britain over the past 30 years, is now rarely seen, other than when re-working an existing pavement.
Slag is an inert fill material of varying size (although some slags may be graded to form selected fills or even Type 1 sub-base material ) and is usually very dense, because of the high iron content.
Ground Granulated Blast-furnace Slag (GGBS) is now in demand as an allegedly eco-friendly cement replacement used in the production of mortars and concretes where it is said to give a tighter, crisper, whiter finish to the cured mortar/concrete.
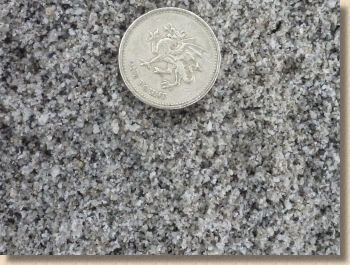

See also....
Slate
Slate is a metamorphic rock, formed when a mudstone, siltstone or other fine-grained agrillaceous sedimentary rock is subjected to supernormal temperatures and pressures. The subsequent change in nature gives slate its characteristic tendency to cleave along parallel planes. This fissile nature and low strength precludes it from being used as a sub-base material , and its tendency to crush to dust under load give it a fairly limited role as a fill material.
Which is a bit of a shame as there are estimated to be 3 billion tonnes of the damned stuff cluttering up the scenery of North-West Wales!
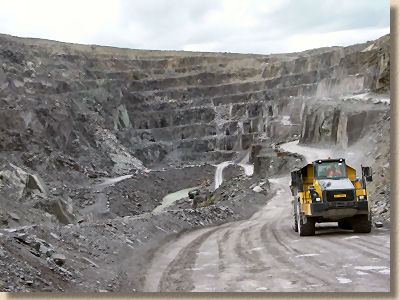
There are two main uses of slate for paving purposes, and both are as surface coverings, rather than as sub-bases or fill materials.
The most common use of slate is as modular paving, as flagstones , either rectangular or irregular in shape, and generally 20-40mm thick. These are laid in much the same manner as pre-cast concrete or yorkstone flags are laid, on a cementitious bed with mortared joints. They are invariably much more expensive than pcc flags/slabs, and, depending on the type of slate, can be even pricier than yorkstone. The primary reason for choosing slate flagstones as a paving is for their colour, usually a blue, purple or green, and/or for their texture.
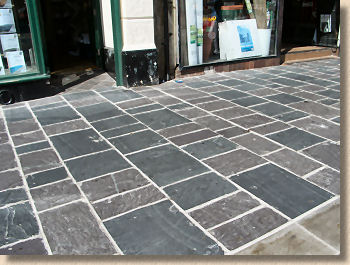
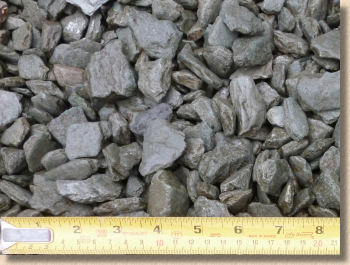
Over the past few years, a new craze for slate has swept the nation and is a real triumph of marketing. Slate mulches are, in fact, slate waste, the offcuts, the trimmings, the unusable dross left over from the roofing slate industries of North Wales and other parts of the country. 15 years ago, the quarries could hardly give the stuff away. And so it sat there, in huge mounds of waste, slowly weathering and supporting absolutely no plant life in its barren state, for year after year until the trendy garden designers latched upon it. Since then, demand has rocketed and it sells for as much as 10 quid for a 40Kg bag - that's 250 quid per tonne, for what is, to all intents and purposes, quarry waste!

See also....
Stone
Stone is by far the most widely used aggregate. It is used in its crushed form as a fill or a sub-base material ; it can be dressed into paving units, such as setts or flagstones ; it can also be dressed into walling blocks , known as ashlar; it can be pulverised and turned into a sand or processed into a cement .
For road construction purposes, there are 11 groups of rocks:
- Artificials
- Basalts
- Flints
- Gabbros
- Granites
- Gritstones
- Hornfels
- Limestones
- Porphyrys
- Quartzites
- Schists
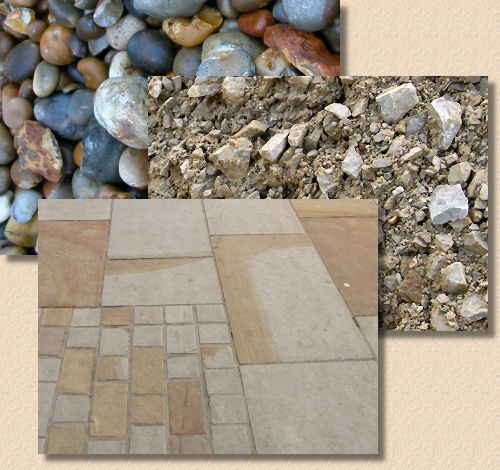
These rocks are subjected to a number of tests, such as crushing strength and polishing value, to determine their usefulness as a road-building material.
Some will be fill or sub-base materials , others will be aggregates for concrete or macadam and asphalt , and a special few will be suitable for surfacing as setts , cubes , flags or kerbs .
Topsoil
The upper layer of soil, usually containing a mixture of clays, silts, sands, grits and humus (organic material). Topsoils vary throughout the country from sandy soils through loams to clay soils. It supports a massive range of flora and fauna and is often placed as a top dressing to earthworks in order to support grasses, trees or other plantings.
Given that there is so much variability in what gets sold as topsoil, there has been an attempt to stipulate what's what and what's not, which is BS 3882:2007 Specification for Topsoil
In essence, the BS identifies three 'grades' of topsoil and sets target values for characteristics such as pH (acidity/alkalinity) and the content of key minerals such as Potassium (K), Phosphorous (P) and Magnesium (Mg).
Premium grade
The best stuff. Screened to remove stones, weeds, roots and other undesirables. Expect to pay a premium!
Medium grade
Pretty good but not the very best. Screened to remove the worst inclusions, but not perfect. Good value for money.
Economy grade
You get what you pay for. In the trade, it's known as "As Dug", which essentially means you get what's taken from the ground with little or no screening. Bit of a lottery, as there are some fantastic 'as dug' soils usually from predominantly agricultural areas, and some stuff that, at best, could be called 'dirt', usually taken from construction sites.
Comparative densities of various aggregates
Material
T/m³
Coverage
m²/tonne
@50mm thick
Notes:
Bitmac - dense
2.31
8.7
See tarmacadams page for coverage rates for different thicknesses and different materials
Bitmac - open
1.98
10.1
Concrete (dry)
2.21
9.0
Normally sold by volume, not weight
DTp1
1.98
10.1
±10% depending on rock type
Gravel - 20-5mm
1.64
12.2
±15% depending on rock type
Grit (4mm)
1.71
11.7
Hoggin
1.75
11.4
Grit sand
1.65
12.1
Topsoil
1.45
13.8
Depends on soil type and moisture content
More data about the densities of various construction materials and aggregates are available on the SI Metric website