Introduction:
Loose, unbound, granular filing for jointing flexible stone pavements has been used for traditional setts and cubes in continental Europe for as long as there have been pavements, while in Britain and Ireland it is experiencing greater use as sawn setts and calibrated flagstones become more reasonably priced and readily available for commercial projects as well as private driveways, forecourts and patios. Loose fill jointing is much more than a matter of simply filling the gaps between paving elements: it is a critical component of the overall pavement and plays a major role in the load-bearing ability of the completed structure.
Loose filling relies on the same principle as the jointing used for flexible block paving , in that a dry, fine aggregate of a specific range of grain sizes is packed into the joints and thereby generates sufficient vertical interlock to maintain the paving elements in place.
Tools:
- Sweeping brush
- Vibrating plate compactor (optional)

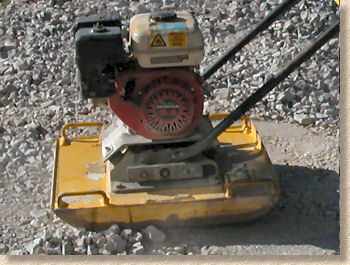
Optional plate compactor
Technique:
This has to be the easiest of all jointing techniques: the loose material is simply brushed into the joints of the pavement and then may be vibrated into place by means of a plate compactor. However, vibration is not always used; it is more commonly employed with smaller elements, such as setts and cubes, and less often with the larger flagstones.
Obviously, this simple technique works best when a dry jointing material is brushed-in over a dry pavement surface. Damp jointing material does not 'flow', preferring to clump together, and so (under normal circumstances) will not completely fill the joint. Similarly, dry material on a damp surface will absorb moisture, rapidly become claggy, and refuse to cooperate.
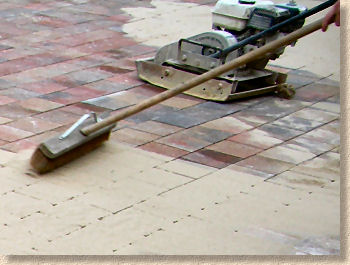
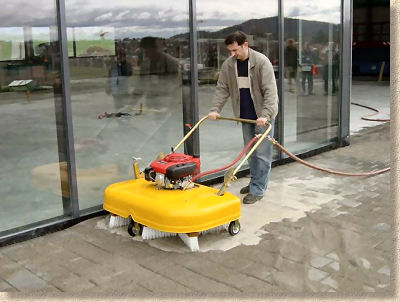
One technique more commonly employed in Europe, particularly during damp weather or the winter months, uses a hose or sprinkler system to wash the fine aggregate into the empty joints. This 'wet jointing' relies on the laying course, and the other sub-layers, being exceptionally free-draining. Should the bedding, for example, retain wash-in water for a period of time, it may result in liquefaction and subsequent movement or settlement of the paving, particularly if a vibrating plate compactor is used to consolidate the paving elements following joint filling.
Materials:
The grain size of the jointing material is determined by the type of paving elements and the width of joint between them. For relatively narrow joints (2-5mm) such as those found with block paving or calibrated setts, a kiln-dried selected sand (2mm down) is normally used. This is NOT just any old sand that happens to be available, and it is definitely not building sand. Both the grain sizes and shape are specifically selected to maximise interlock and therefore an inappropriate sand may actually weaken the designed strength of the pavement.
For slightly wider joints (4-10mm) a crushed hard-rock aggregate known as "splitt" is normally used. This material is approximately 4mm down and often made from a crushed granite, basalt or diorite, rather than from rock of a sedimentary origin. On some projects, splitt or grit jointing may be topped-up using a limestone dust, as this will loosely bind together the uppermost few millimetres of the jointing and help minimise loss to scour during the early life of the pavement.
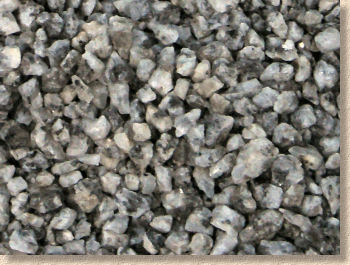
Coverage:
Actual coverage for the jointing material varies enormously depending on joint width and depth. Tight-jointed sawn setts require significantly less jointing material per unit area than cropped setts or fettled-edge flagstones.
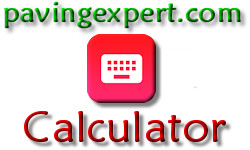
Use this Pavingexpert Calculator to determine approximate coverage for loose-fill jointing
It is common for jointing material to settle over the first few months, regardless of how well vibrated it might have been when placed. Further, before the loose material effects a natural 'seal' of detritus, it is vulnerable to scour from wind, surface water, and sweeping/cleaning, which can remove some of the loose material and, in extreme cases, completely empty the joint.
Consequently, it is essential that the pavement is inspected every 2-4 weeks during the initial 3-6 months following construction and that the joints be topped up as and when required. In areas experiencing heavy surface water flows or on civic pavements subjected to vacuum/brush street cleaning equipment, it may be beneficial to use a joint stabilising product or even a paving sealant to bond together the sand/aggregate and give it more of a chance to resist the scouring action found in these unfavourable conditions.
Examples:

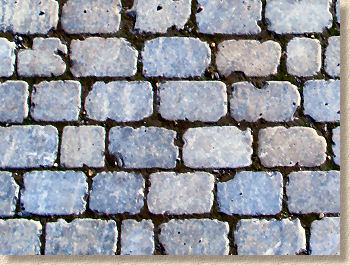
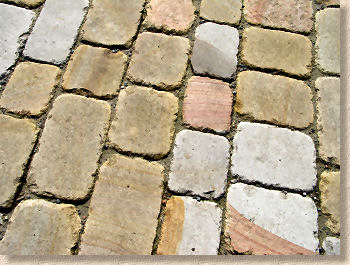
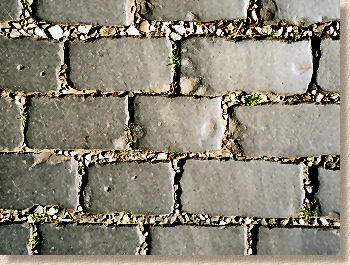
Comments:
Loose aggregate is the original jointing material for all segmental pavements. The ancient Sumerians, the Chinese, the Greeks and Romans all relied on coarse sand, fine gravel or crushed rock to fill the gaps between their paving elements. They may or may not have understood the physics involved; it's quite likely it was done solely to prevent individual elements from wobbling or rocking (what we now tend to refer to as "rotation"), but the fact remains that loose aggregate fill has been used to joint pavements for as long as humans have built them, and it still has a role with modern paving. One need consider only the many millions of square metres of block paving that are 'locked together' by loose sand for proof of that!
Despite its pedigree, loose jointing is not suitable for all modern pavements. It doesn't cope terribly well with high speed vehicular traffic, and it is prone to scour from wind, rain and surface water, but it's the most cost effective jointing method and material for low-speed, light-to-medium duty pavements such as footways, piazzas, patios and driveways.
It's minimal cost and stain-free installation is helping to make it a popular choice for modern footpaths and civic squares, but the risk of jointing loss due to over-rigorous street-cleaning regimes can compromise the integrity, and longevity, of the pavement, and so some form of joint stabilisation really ought to be considered in such applications.
Other pointing and jointing pages...
- Introduction
- Terms & definitions
- Pointing Styles
- Spacers for Paving
- Cement Mortars
- - Hand Pointing
- - Pointing Riven Flagstones Using Coloured Mortar: A Case Study
- - Wet Grouting
- - Dry Grouting
- - Slurry Grouting
- - Gun Grouting
- - Poured Grouting
- Resin Mortars
- - Polymerics
- - GftK Polymerics: A Product Study - VDW 840+
- - Romex Polymeric Mortars: A Product Study
- - Jointex Polymeric Mortar: A Product Study
- - Slurries
- - GftK Slurry Mortars: A Product Study - VDW 800 Permeable
- - GftK Slurry Mortars: A Product Study - VDW 850
- Re-jointing paving
- Pitch Jointing
- Loose Fill Jointing
- - Stabilisation
- Alternative Jointing Materials