Introduction:
A more general overview of the use of tarmacadam/bitmac is given on the Tarmacadam Basics page and a case study of the actual construction methods for a footpath/driveway can be found on the Laying Paths & Driveways page.
The construction methods considered in this section refer to three typical small projects - a footpath, a residential driveway and an access road for small-medium vehicular loads. For heavier applications, you should consult a reputable local contractor, or email us for a more detailed construction specification.
The construction of a typical bitmac footpath is covered in more detail on the Laying Drives and Paths page.
There should be at least 4 layers to all bitmac pavements:
- Surface course
- The top layer of bitmac providing the running surface
- Binder course(s)
- The first layer of bitmac
- Sub-base
- A load bearing layer of crushed rock
- Sub-grade
- The ground beneath a pavement, stripped of all vegetation and topsoil
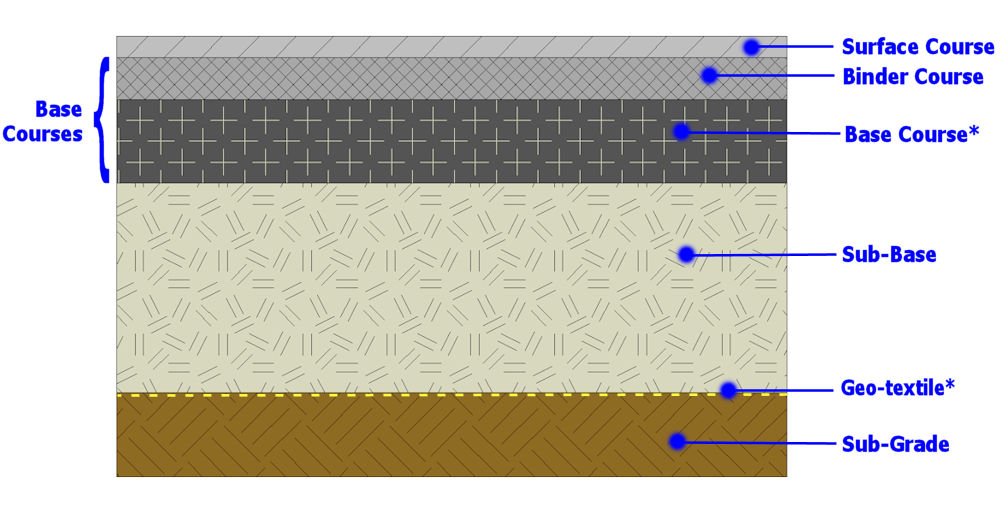
The sub-base and base courses may be constructed from more than one individual layer of the specified material, but for our purposes, we will consider each layer as being a single entity.
Sometimes, levels permitting , an existing bitmac or concrete surface can be overlaid with a new surface course. This is acceptable provided that the new surfacing is properly bonded to the old surface. It is not good practice to overlay existing flags/slabs. Overlays are considered in more detail on the Tarmacadam Basics page.
Construction Method
Mark out the site. It is assumed that the surfacing is to be flush i.e. level, with the existing ground. It is a good idea to excavate wider than the planned width, allowing an extra 300-450mm at the edges makes handling much easier, especially if kerbs are to be used.
See Setting Out page.
In most cases, a well-laid tarmacadam surface is impermeable to water, and should be constructed in such a manner that surface water will be directed to adjacent open ground, a gully or similar drainage point.
Bear in mind that private driveways are not permitted to drain onto a public highway or directly into the sewer system. See the Draining Pavements page for further information.
There are pervious or permeable bitmacs available from the batch plants, and while they do have their uses, they are not considered any further in this section.
Excavation
The surface needs to be dug off to a depth of at least 175mm. The depth of dig can be roughly calculated as....
(surface course + binder course + sub-base)

So, for the three projects under consideration, the dig depth is given in the table opposite. All figures are in mm and are typical values we have used for bitmac work in the past 30 years. Conditions in other parts of the country vary and a local contractor may suggest differently, based on their experience.
All weeds and other unwanted organic matter, along with topsoil must be removed and any soft spots excavated and filled with compacted sub-base material. If the area is troubled with weeds, it should be treated the excavated sub-grade with a general weedkiller such as Glyphosate, but it is unlikely any weed will be able to penetrate the upper layers. A Geo-membrane can be used if deep-rooted, pernicious weeds are a problem, of if there is any concern regarding the competence of the sub-grade .
Edgings or kerbs MUST be used on free edges, i.e. those parts of the perimeter of the surfaced area not bounded by walls or other solid structures that will act as a retainer for the bitmac. This is to prevent the bitmac crumbling at the edges, as shown in the photograph opposite. Brick edgings, plain or decorative edging kerbs, or setts laid lengthways are all suitable, and should be constructed at this stage.
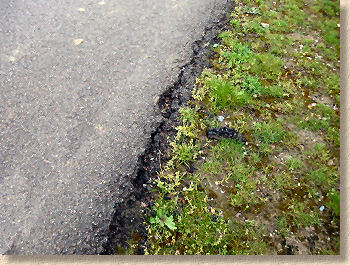
Sub-base
This is essential if the pavement is to last longer than a couple of years. Do not employ any contractor who tells you that a sub-base is not required, unless there is a suitable existing sub-base or base layer. The sub-base should be a minimum 100mm thick. Refer to the sub-base page for full details on installation of a sub-base.
Binder course
This is a load-bearing, strengthening layer of the pavement and should be at least 40mm, preferably 50mm thick. The material used as a binder course is 'chunkier' than a wearing course, usually comprising 20mm or 28mm aggregate in a bitumen binder, known as Dense Bitumen Macadam (DBM). On public highways and other heavier-use projects, the binder course may be underlain by a base layer.
For binder course 50-80mm thick, use 20mm material (DBM) For binder course 70-150mm thick, use 28mm material (DBM)
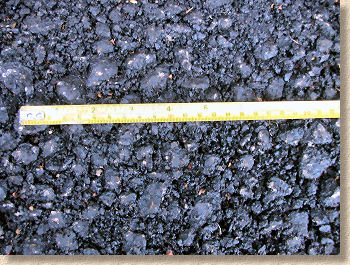
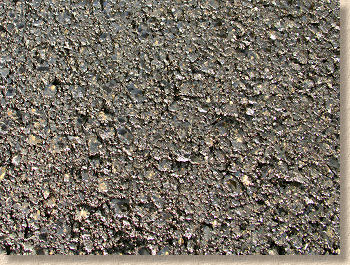
The binder course material should be laid and levelled out reasonably level (± 10mm) and thoroughly rolled and compacted before preceding with the wearing course. Larger areas may be laid by a paver machine specifically designed to lay bitmac. This usually gives a 'truer' i.e. more accurately levelled, surface than hand-laying.
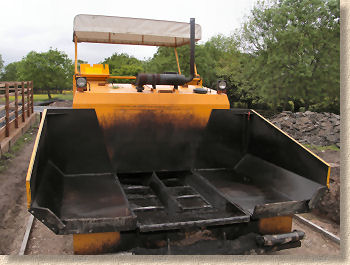

Sealing Grit
When the surface course is to be laid immediately following, or a short time after the base course, the two layers will bond together naturally. However, if there is to be a significant delay (more than 1 week) between completing the base course and laying the wearing course, the base course should be sealed with a sealing grit designed for this purpose. Sealing grit is made up from bitumen-coated grits of approx 3mm down that is spread over the compacted surface and brushed-in to fill any voids in the base course and thereby prevent them being filled with mud or other unacceptable contaminants.


Prior to final surfacing with the wearing course, which may be several weeks or months later, the base course needs to be painted with a bonding emulsion to ensure proper adhesion.
For more information, see the notes on overlays on the Tarmacadam Basics page.
Surface course
This is the top layer of the bitmac pavement, the layer that is seen and trafficked. It needs to be fairly regular to provide a smooth ride for wheeled vehicles, although this is much more important on higher speed pavements than on residential driveways. A macadam surface course should consist of a small, hard aggregate, usually 6mm or 10mm, in a bitumen or asphalt binder. Alternatively, an asphalt may be used; this material is also known as a sand carpet or asphalt carpet, and is prepared in a batch plant to a specified recipe, consisting of selected sands and grits mixed into an asphalt matrix, with coated chippings sprinkled over the surface and rolled into the asphalt as part of the compaction process. Again, it may be machine or hand laid, depending on area and access.
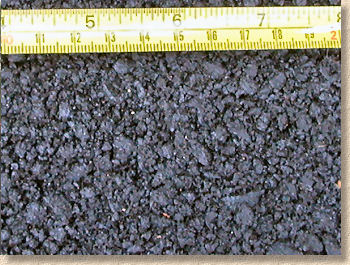
The wearing course should be at least 20-25mm thick when rolled, and should not deviate from the correct level by more than ± 6mm. There should be no roller marks in the finished surface. We recommend a minimum fall of 1:80 for tarmac areas, although a fall in the range 1:40-1:60 is preferred.
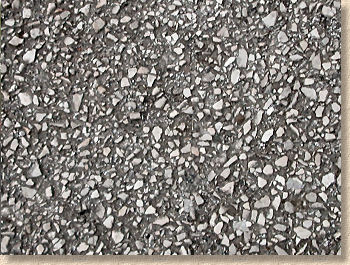
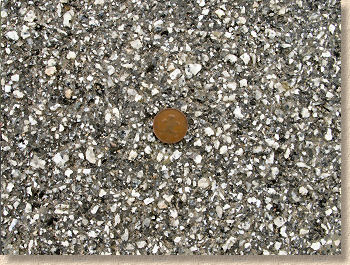
Surface courses that use limestone or other light coloured aggregates will wear over time to give a greyish appearance to the surface, as the tar binder is gradually eroded by traffic and exposure to the elements, to reveal the grey-white aggregate.
Hardstone based macadams, such as that shown above, are generally much darker, relying on a basalt or other hard, dark aggregate, and so when they wear and weather, they tend to remain dark in appearance.
A Touch of Colour
Coloured macadam surface courses are available in two basic types. In the cheaper type, the binder (tar/bitumen) is coloured (e.g. red), but the aggregate is the same as for a normal black wearing course, e.g. a limestone or hardstone. This type of wearing course may well lose its colour over time when the aggregate becomes more and more exposed as the binder is gradually worn away.
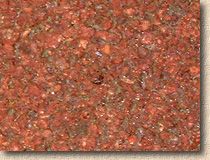

The best quality coloured wearing course material will use a coloured aggregate that matches the colour of the binder. For example, a good red wearing course will comprise a red binder with a red aggregate, such as quartzite. Then, as the binder weathers, the aggregate will ensure the surface doesn't lose the colour for which you have paid a lot of money!
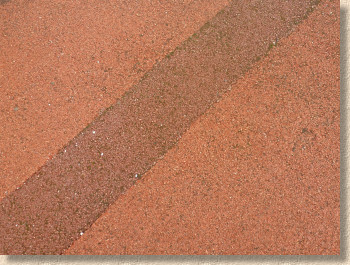

The latest developments in binder technology have now made available highly coloured wearing course materials, such as the stunning red, gold and green surfacing supplied by Bardon Aggregates to the Millennium Dome and Buckingham Palace in London.
Although this ability to create custom colours for individual jobs has not yet filtered down to the 'average' residential driveway market, it is predicted that these new colours could reclaim some of the civic paving market that the bitmac manufacturers have lost to block paving over recent years.
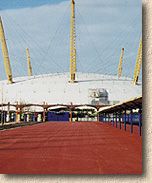
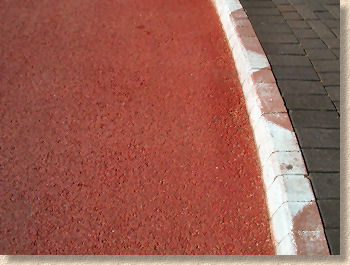

It should be noted that coloured (ie: non-black) macadam is relatively expensive, especially so on smaller projects such as residential driveways. Red macadam is the cheapest of the coloured options, while specialist colours such as buffs, blues and greens, can be scarily pricey.
It's not simply a matter of coloured macadams costing more because pigmented binders are more expensive, and the potential additional cost of a specially coloured aggregate, the batching plant will often impose a charge for cleaning the plant of the usual black, and also for cleaning any wagons used to carry a coloured 'mac, especially the paler colours, and then there could be an additional charge to clean the plant of the coloured material before they switch back to the standard black product.
Individual projects need to be costed individually, but it is not unusual for costs on a typical 60m² residential driveway to be + 30% for a red macadam and as much as +100% for some of the paler colours.
Obviously, with larger projects (greater than around 300m²) the additional costs for coloured macadams are not as severe, but they are still pricier than black.
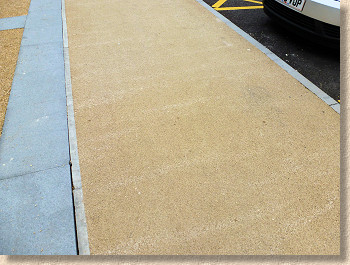
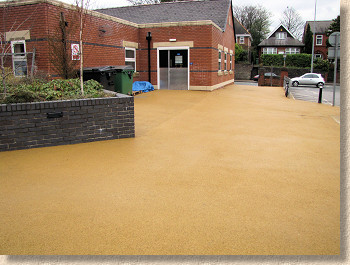
HRA
Hot rolled asphalt (HRA) may occasionally be used as a surface course on footpaths or driveways. This is a very fine-grained material, more commonly used on public highways, and relies on the presence of embedding chippings of a hard stone to improve durability and to add traction.
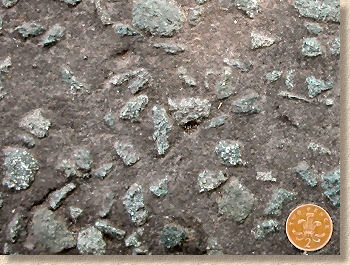
Once the asphalt has been spread out and levelled, usually by machine and to a thickness of 40mm, the pre-coated chippings are scattered over the surface at a specified rate (Kg per m²) and rolled into the asphalt to improve skid resistance.
The chippings must have both a high Polished Stone Value (PSV) and a low Aggregate Abrasion Value (AAV). The high PSV ensures the chippings don't become 'slippy' when worn, and the low AAV ensures a good resistance to abrasion (wear). Consequently, over a period of use, the chippings tend to stand slightly proud of the worn (abraded) asphalt matrix, which is much softer, comparatively.
The chippings may be artificially coloured by coating them with a pigmented binder, or they may rely on the natural rock colour, eg a red granite, to introduce colour to the surface. In all cases, the chippings are pre-coated to ensure proper adhesion to the surface layer. Uncoated chippings are NOT suitable.


On the subject of chippings, these are sometimes added to residential driveways for decorative purposes. However, there are a couple of drawbacks with this practice. Un-coated chippings will not adhere properly to the wearing course, and, with macadam (rather than HRA) surface courses, there is a problem ensuring the chippings are properly rolled into the surfacing material and thereby held firmly in place. For this reason, we prefer not to use chippings on this type of work, but, if required to do so, a 3-6mm fine-grained dense macadam wearing course would be used and lightly sprinkled with the chosen chipping which will generally be 6-10mm in size. The practice of scattering 18-20mm unwashed limestone chippings over a 6mm or 10mm macadam wearing course is not recommended and is often a trademark of the cowboy element.
Finishing-off - Rolling
All bitmac and asphalts are consolidated by rolling. In most cases, a mechanical roller suitable to the size of the job will be used. This may be a single-drum walk-behind roller, a ride-on twin-drum roller or, on the larger jobs, a full-sized, triple-drum road roller (still fondly referred to as a "Steam Roller" by some members of the public). All modern rollers offer a vibratory option, which can be useful to ensure thorough consolidation but needs to be used with care on wearing courses at it can result in causing the drums to skid which may mark the surface.
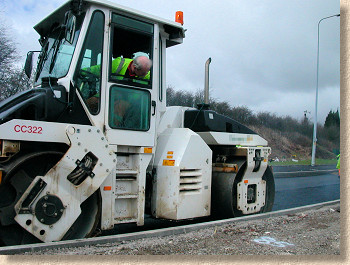
THIS is a Steam Roller!
Only in very constricted areas will a hand-roller (pulled or pushed by the operatives) or vibrating plate compactors (wacker plates) be used. However, an asphalt punnel may be used around edges, gullies, manholes etc. to hammer down the surfacing to the required level.
Surfacing should be sufficiently cool and hard enough to be trafficked 1-6 hours after being laid. However, some hand-laid bitmac contain a ' cutback ' agent that retards the setting and may need to be left overnight to thoroughly cool and harden.
The construction of a typical bitmac footpath is covered in more detail on the Laying Drives and Paths page
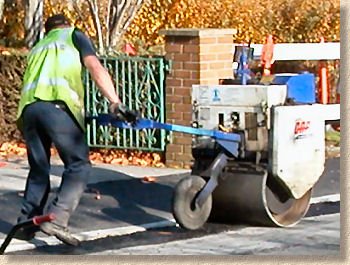

Jointing Bitmac
A surface course on a footpath or driveway is usually laid as one expanse of bitmac, however, there may be situations where the new surface course is to abut an existing surface, or where the final surfacing can not be completed in one operation. On wider areas, the surfacing may be laid as a number of parallel strips or screeds, each 2m to 6m wide.
When adjacent screeds are laid sequentially with no delay or more than about an hour between the two passes, the seam may be left untreated, with the slightly newer bitmac being laid against the slightly older material and the two rolled as one, relying on the still-tacky binder to form a sound joint.

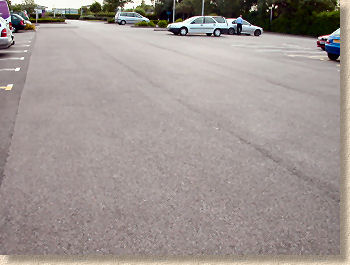
In situations where there is a delay between laying adjacent 'screeds', or when new material is laid against an existing surface, the 'joint' between the two surfaces needs to be sealed and protected to prevent the ingress of water, where a freeze/thaw action can result in the surface course being 'lifted' from the base beneath. The edge of the older layer should be neatly cut and then primed with a vertical jointing compound. Once the new material is laid and compacted, the resulting joint should be sealed with a proprietary compound, referred to as 'cold pour' or similar, or a "sealing tape" often referred to as 'Overbanding'. Where a multi-layer pavement needs to be jointed, the joints need to be staggered by 300mm, not created as a single full-depth joint through the pavement.


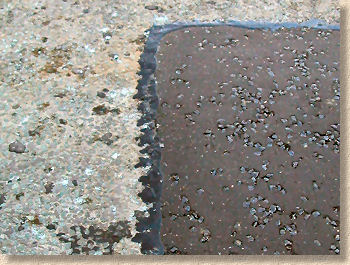
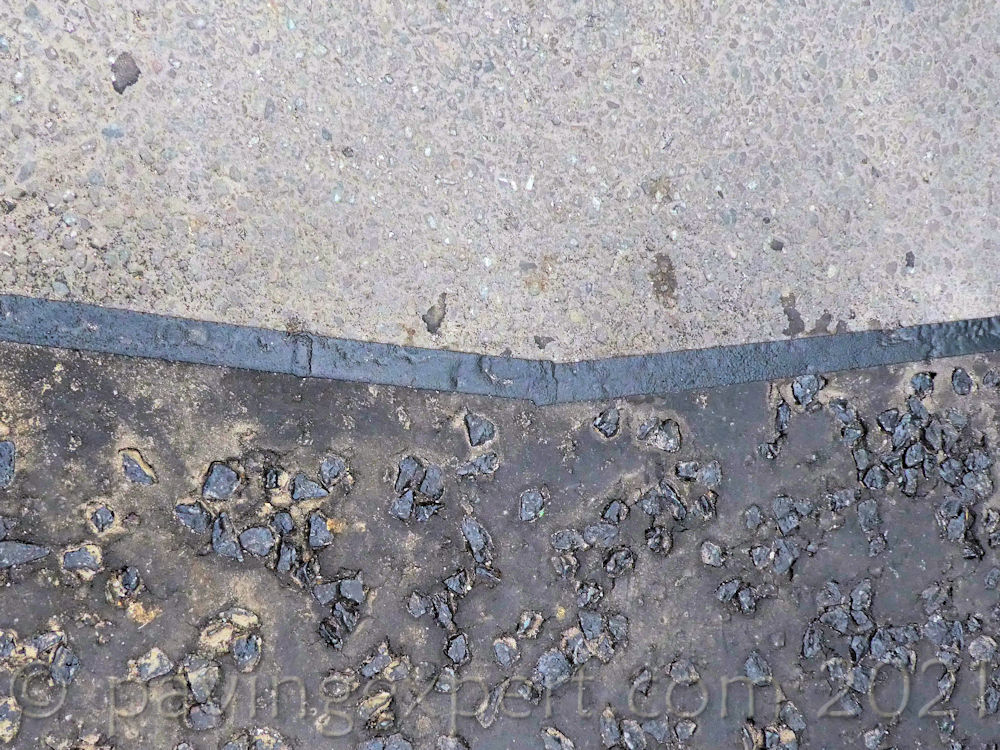
Coverage Rates
Coverage rates are variable according to the thickness of each layer. Bitmac and asphalt are sold by weight and the standard coverage rates we work with are...
- 25mm of 6mm dense wearing course - 15-19 m² per tonne
- 40mm of 10mm dense wearing course - 10-12 m² per tonne
- 50mm of 20mm open base course - 9-12 m² per tonne
- 50mm of 20mm dense base course - 8-10 m² per tonne
- 65mm of 28mm open base course - 7½-10 m² per tonne
- 65mm of 28mm dense base course - 6-7½ m² per tonne
Handy coverage calculator from Midland Quarry Products
Construction Diagram
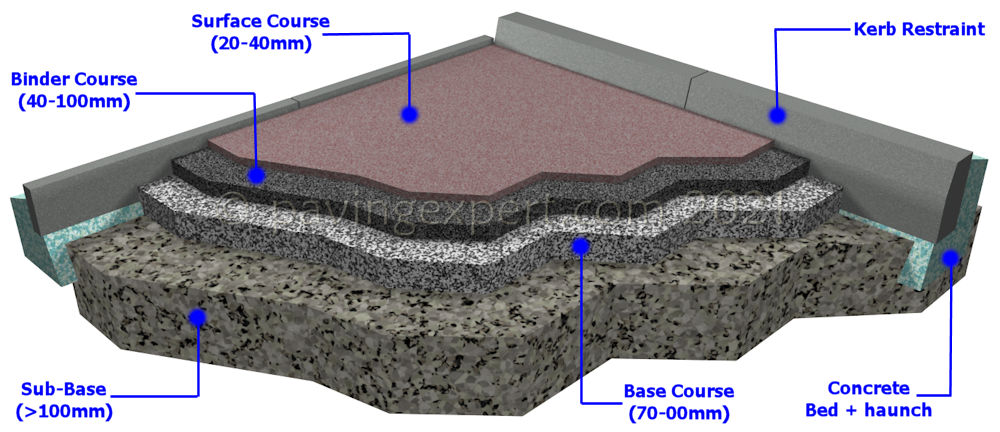