Machine-laid clays?
A month or so ago, one of the Brew Cabin Irregulars posed the question of whether there was any future for block paving, and during the ensuing discussion the point was made that two relatively new developments would ensure block paving would be with is for many, many years to come: permeable pavements and machine-assisted installation. Although the original poster was primarily concerned about concrete block paving, it's an equally, if not more, valid consideration for clay pavers. More or less since the first concrete block was de-moulded and shunted into a curing chamber, they've had the lion's share (and a fair old chunk of the elephant's portion) of the market for small segmental pavers. Consequently, if the concrete wallahs are staking their claim to the permeable and/or machine lay market, then the clay chaps need to be in there, too.
Which is why I'm out in the rain on a cold November morn, witnessing what was the world's (well, definitely Wem's) first ever machine assisted installation of a permeable clay brick pavement.
This is a collaborative effort between Probst UK , purveyors of excellent machine lay equipment, and Blockleys , widely recognised as one of the country's premier producer of quality clay pavers. As luck would have it, both companies are based in Shropshire, and Probst had available a reasonably sized trial area that needed paving. So bring on the pavers!
The trial installation would use Blockley's innovative Hydrosmart ™ paver system laid using a custom lifting head carried by a Probst Robotech machine.
This is very much a trial, and as such, a number of headaches were fully expected. After all, the purpose of a trial is not simply to see how well a product or technique performs, but to find out just what can go wrong, and how said product/technique can be improved. I think it's fair to say that, over the course of a couple of days, more was learned about the intricacies of machine-assisted installation of clay pavers than had ever been imagined.

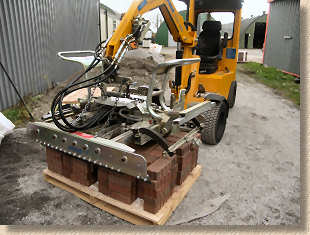
From a manufacturer's point of view, arrangement of the layers, packaging, and palletising all presented new challenges, while the handling kit had to cope with the clay pavers that are slightly larger than normal (210x105mm rather than 200x100mm), that are not prefect rectangles, and feature extra-large spacer nibs on three sides and none at all on the fourth.
Just setting-up the lifting head involves quite a bit of tweaking and adaptations to find the best 'fit' for the clay pavers. The 90° herringbone format doesn't help; a 45° layout might work better, and I suspect that will be tried at some point. As always with clay pavers, maintaining a decent alignment is half the battle, and it doesn't seem to be any easier when the blocks are placed by a machine rather than a human hand.


Progress on Day 1 was slow; but then it always is at the start of any job. By lunchtime, the weather had taken a turn for the even worse, and with discretion being the better part of valour, I beat a hasty retreat to my nice, warm, draught-proof office. While Day 2 was slightly less damp, the wind was as thin as a feeler gauge and cut right through you. Happily, the speed of laying had increased dramatically, and by the time Blockleys' Technical Manager, Ian Cook, turned up, each panel was being dropped into position in a little over a minute: still a good way to go when compared to other machine-lay cycle times, but a significantly improvement on the previous day.


Overall, this was a strange experience, a mixture of excitement and frustration. It's wonderful to see someone having a go at machine-laying clay pavers, as it's an immense engineering challenge and one that really needs to succeed if the clay industry is to maintain or even expand its market share, but the slow pace is finger-gnawingly frustrating to an ex-contractor. While it's fully accepted that the laying speed was never going to be spectacular on a trial project such as this, my contractor's innate instinct for losing money tells me that we need to be shown a system that is significantly faster than hand lay if the technology is to be adopted by the wider industry. If you had to choose a team to resolve the problems presented by clay pavers, Blockleys and Probst would, pretty much, be the dream choice, so if anyone can crack this particular nut, it will be them.
The Probst lifting head clamps onto one layer of pavers, aligning them and grabbing them securely before lifting them and carrying them to the laying face
The lifting head carries the Hydrosmart pavers to the laying face and places them against the already laid pavers
PS: An electrically powered block splitter was used to cut the pavers on this project - read more about this in the "Where's me maul?" blog