Introduction:
The same principles apply whatever type of stone is used, although some of the sedimentary types (sandstones in particular) can be far more porous and may need a slightly damper laying course and a wetter bond bridge.
Urban settings bring special problems to flag laying, and over recent years it has been realised that the older, more traditional methods of laying streetscapes have been less than successful. In particular, the materials used for laying course and jointing have been re-thought and most public work will now use proprietary bedding and an approved jointing material, rather than the site-mixed 'twenty-to-plenty' mortars of yesteryear.
Sub-layers:
Sub-base, Base and/or Roadbase:
More consideration is now given to the sub-base . On some projects, a standard unbound sub-base of Type 1 or 804 material will be used, but a growing number of projects are using bound bases of dense bitumen macadam (DBM) or cement/hydaulically bound material (CBM or HBM) , particularly beneath footpaths that are likely to experience vehicle overrun, whether it is planned as in access to off-road parking, or unplanned, as happens when cars are 'bumped up' the kerb and parked with two wheels on the footpath while the driver nips in to a local shop for a lotto ticket.
Sub-bases and base layers are now designed as part of the overall pavement structure. Good guidance is given in BS7533:12
Laying Course:
As mentioned above, laying course materials are often proprietary products which meet the requirements of Table 3 of BS7533:12 which requires a compressive strength of not less than 30N/mm² and an adhesive strength greater than 2N/mm².
However, some bedding systems use materials that do not meet these requirements, but which offer other advantages that the pavement designer considers to be more desirable. For example, some designers prefer to have the more porous granite pavings (eg: G603) laid onto a no-fines bedding because this is considered to eliminate the risk of moisture being in contact with the underside of the paving units and thereby reduce the risk of unsightly damp patches or picture framing.
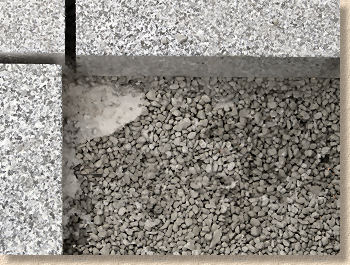
As always, the British Standards and the EN equivalents are recommendations . They generally indicate best practice but cannot take into acount every conceivable factor that might affect a pavement design.
Other materials for use as a laying course are considered on this page
Slurry Coat - Primer - Bonding Bridge
Various names are given to this technique and there are almost as many theories as to why it is done. In essence, the underside of the paving unit to be laid is coated with a cementitious slurry just before being laid onto the prepared laying course. While some refer to it as 'slurry'. it is also known as "Primer" and some engineers like to refer to it as a 'Bonding Bridge".
The most plausible explanation for its use is as a bond bridge, that is, an adhesive layer between paving and laying course intended to ensure a firm bond between the two, creating a rigid and firmly bound pavement structure. However, it is also promoted as a method of preventing a 'thirsty' paving unit dewatering the laying course and thereby creating a plane of weakness at the interface between paving and laying course. Whilst this is technically credible, to then use a bond bridge slurry with a semi-dry laying course defeats the logic of using it in the first place!
Whatever the engineering theory, the fact remains that most rigid construction stone pavements are now laid in this way.
The actual 'slurry' varies from job to job. There are a number of proprietary products which all seem to be minor variations to a base recipe of cement, SBR , plasticiser and sulphur fume. Some projects use a simple site-prepared mixture of cement with liquid SBR.
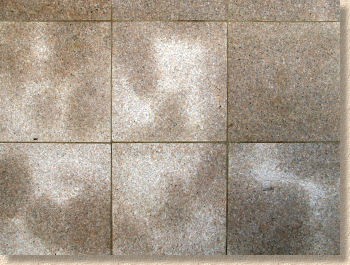
There are also claims that PVA will perform the same function: this is not wholly accurate. Using PVA or a PVA-cement slurry as a bond bridge will not create anywhere near the degree of adhesion and bonding that is engendered using SBR, and there are concerns that PVA is neither water- nor frost-proof. It seems that the PVA myth has gained ground amongst patio and driveway contractors as a cheap alternative to using SBR or an SBR-based product. There is also some anecdotal evidence that use of a PVA primer reduces the incidence of damp patches with porous granite paving. While some contractors swear by this technique, it has never, as far as I'm aware, been proven in field or lab tests.
The slurry primer (or whatever the hell you want to call it!) is normally applied using a small hand brush or, with some of the thicker slurries, using a float trowel. Enormous care is required to ensure none of the slurry is allowed to stain either the paving being primed or any of the surrounding area. SBR slurries stick like the proverbial s-h-one-t to a blanket, and once hardened, which may take only 10 minutes, are virtually impossible to remove. Any spillages MUST be wiped with a wet cloth immediately (if not sooner). It's also advisable to wear gloves when working with SBR slurries as it WILL bond to bare fingernail and remain there until it grows out.
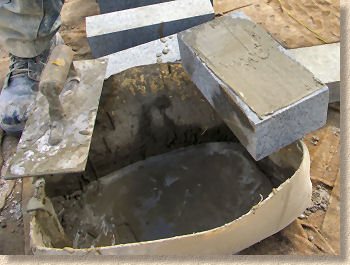
The hows, whys and whats of using a bond bridge (or slurry primer if you prefer that phrase) are considered in greater detail on a separate page .
Laying Procedure
The actual process of laying is much as described elsewhere on this website : a bed is prepared, the flag is placed, and then it is consolidated by tapping down to level using a rubber maul or mallet.
Laying course material is prepared in a mixer, adding water to create a consistency ( slump ) that suits the laying operative. Some paviour's prefer a 'just damp' mix, some prefer 'moist', while others insist on a wet mix. There is no right or wrong: it's a matter of personal preference. However, the wetter the mix, the messier it becomes, and with larger, heavier flags there is a problem of flags 'floating' on the saturated bed. Most professional contractors will use a damp or moist mix.
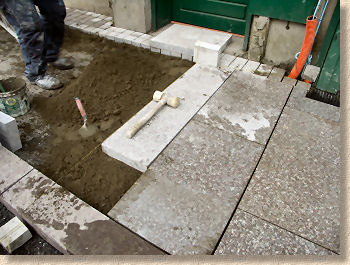
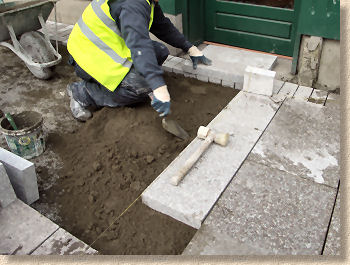
Once mixed, the bed material has a working life of an hour or so, so it is normally mixed 'on demand' and brought to the laying face in a wheelbarrow. Most paviors will work from the base rather than from the laid paving, as it is relatively easy to disturb freshly laid flagstones. Consequently, only sufficient bed material to accommodate the next flag or the next course of flags will be put out at any time, so that the laying operative is not standing or kneeling in cementitious material.
Most street-quality flagstones tend to be calibrated with a tolerance better than ±2mm, and so some pavior's will choose to screed the bed rather than prepare individual beds . Obviously, some of the riven flagstones and reclaimed paving will not be calibrated and therefore individual bed preparation is the only option.
When the bed is ready, the bond bridge slurry will be applied to the underside of the flagstone immediately before placing it onto the bed. Smaller flags are lifted into position, while heavier flags are normally lowered from a long edge . Flags weighing more than 25kg may be lifted into position by two operatives often using a mechanical or vacuum lifting aid .
For projects where a regular, consistent joint width is required, the use of paving spacers is often the best option.
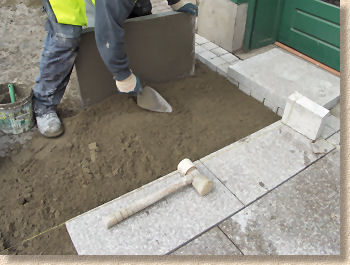
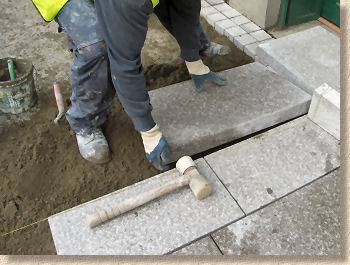
These flags will be jointed at a later date using a cement mortar slurry , therefore the joints need to be kept open and regular. Some tradesmen will use wooden or plastic spacers to ensure regular joints but others find that the small differences in plan sizes can cause problems when a consistent joint spacer is used and so they prefer to manually set the joint width which allows them to accommodate minor variation in length or width.

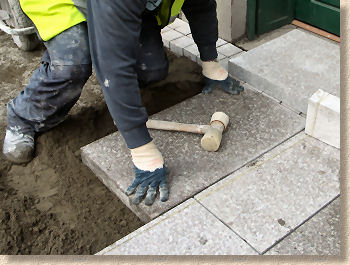
Once in position, the flag is tapped down to level and consolidated using a rubber mallet or maul. The aim is to create a firmly compacted full bed first time - liting and re-bedding the flag wastes time, reduces productivity and therefore reduces wages.f
The flag is checked for stability using the diagonal rock test, where diagonally opposite corners are pushed to see if there is any movement.
Laying will continue until a section is completed and then the gang may spend a day slurry jointing before opening the pavement to the public.
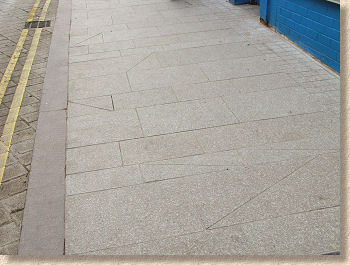
Many public works have a 'lip' tolerance (that is, the maximum level difference between two adjacent paving units) of 2-3mm, and so on street reconstruction work where there is limited control over levels and thresholds, it is often necessary to diagonally cut flagstones to 'fold' them and so avoid lips. This can become unsightly when too many flags are cut in this way. It may be possible to avoid some of the cuts by choosing smaller flags. For example, where a 600mm wide flagstone has been diagonally cut and folded, it may have been possible to avoid any diagonal cuts by using two 300mm wide units and allowing the additional joint to accommodate to level difference.
Typical rigid street paving construction cross section
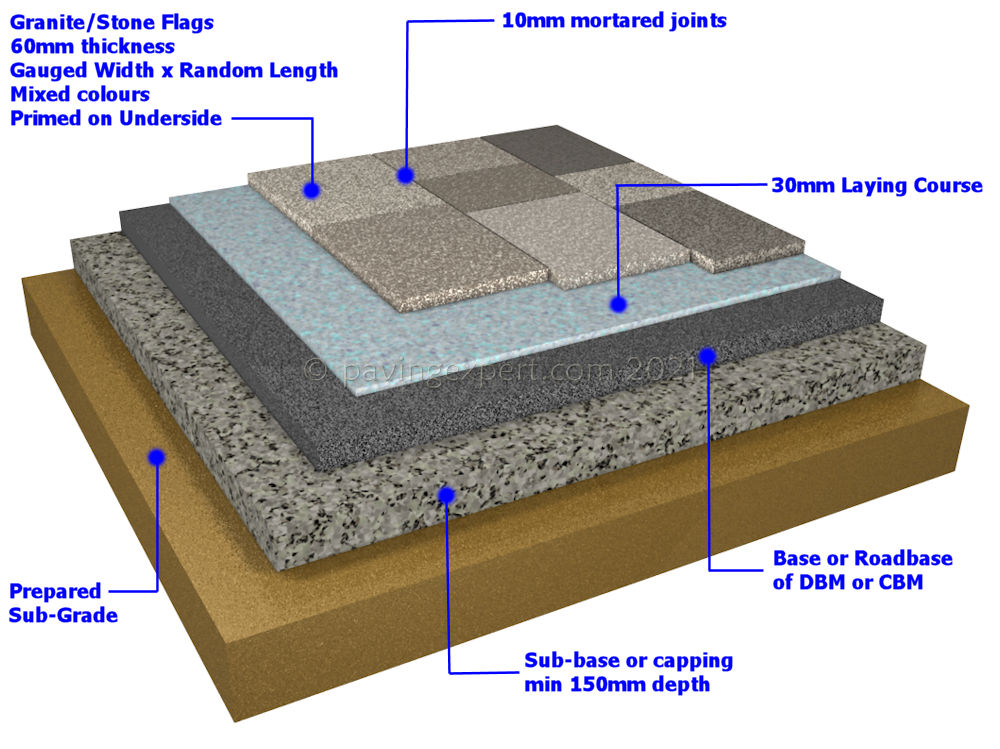