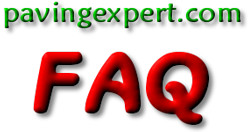
When you've laid your edging courses and all your sub-base etc, at what height do you lay the block pavers above the edging blocks to allow for them to be whacked down?
Introduction:
This is one of those questions that DIYers ask again and again because they think there must be a simple answer. If only it were so!
What they are asking about is the screed depth: at what depth below the top of the edge courses does the screeded laying course material need to be to accommodate the paving prior to final compaction?
The key point to understand is that Screed Depth (D) is not and should not be the same as Paver Thickness (T). The unconsolidated paving, laid directly onto the prepared screed bed, needs to be higher than the fixed edge courses so that consolidation with the plate compactor will settle them down to the correct level.
As mentioned elsewhere, there needs to be some 'give' in the laying course sand to accommodate the minor differences in thickness that occur in even the very best pavers, and it's tempting to think that, if all the paving was to be laid onto a screeded bed that was established at, say, 6mm high, then the consolidation work with the vibrating plate compactor will rattle them down to the required level.
Complications:
Why it's not so straightforward
The problem is that there are so many variables affecting how the laying course material will compact:
- type of laying course material
- depth of laying course material
- moisture content of laying course material
- method of preparing screed
- thickness of paver
- type of paver
- type of sub-base
- tightness or otherwise of sub-base
- presence or otherwise of geo-textile between sub-base and laying course
- type and efficacy of compaction equipment
- ... and probably what colour of socks you're wearing!
Laying course variables:
The type of material used for the laying course has a direct bearing on how it compacts. A Mersey Grit will compact differently to a crushed rock sand will compact differently to a whinstone grit.
It should also be readily obvious that the depth of the laying course will affect what screed depth is needed. If the screeded laying course prior to placement of the paving has an overall thickness of, say, 30mm, it may compact to, say, 25mm so the blocks would need be laid with a 5mm surcharge. However, a 50mm thick screeded laying course may compact to, say, 41mm, which would require the paving to be laid with a 9mm surcharge.
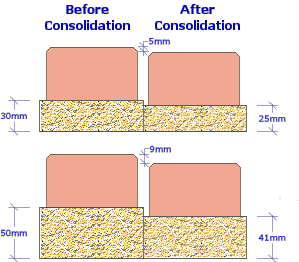
Less obvious may be the effect that the moisture content can have. A typical grit sand with, say, only 5% moisture content will compact differently to the same sand when it is dripping wet with a 20% moisture content. The likely difference in a 40mm screed may only be a millimetre or three, but when combined with other factors from this list, that could be enough to cause a puddle in the completed pavement.
Back to the blindingly obvious - the method of screed preparation. The three acceptable methods were described on the main screeding page and it should be apparent that a bed prepared using the pre-compaction method will not compact as much as one prepared using the partial pre-compaction method, which, in turn, will not compact as much as an uncompacted bed.
Paver variables:
It should be even more blindlingly obvious that the thickness of a paver has a major impact on the required screed depth. A 60mm paver will not require as great a screed depth (D) as an 80mm paver - s'obvious, innit!
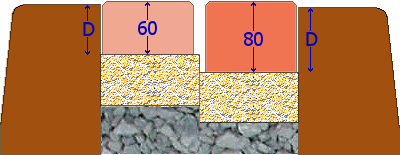
However, the type of the paver also has a minor influence on the behaviour of a screeded laying course, and, as already stated, minor influences may combine to create major problems. It's partly to do with the plan size of the blocks or flags (smaller pavers transfer the compaction force more effectively than larger pavers) and partly to do with the texture and/or condition and/or base shape. For example, tumbled pavers tend to have chewed and battered vertices and these can provide space into which the bedding material could be shifted. It's a minor effect, but relevant, nonetheless.
Sub-base variables:
The laying course typically lies directly over the sub-base (or, in some cases, directly over a base course). The type of material used to form the sub-base (or base) will have a minor effect on the eventual compaction of the laying course and the consolidation of the pavers, as some rock types are more 'resilient' to compaction, and some sub-bases will have been fully 'compacted to refusal' while others may still have a couple of millimetres of so to go.
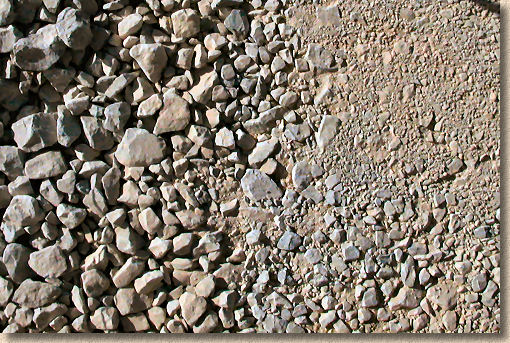
Of more concern is the 'tightness' of the sub-base surface. Best practice requires that a sub-base should have a 'tight' or 'dense' finish; that is, there should be few or no voids apparent on the surface of the compacted sub-base into which laying course material might 'trickle' either as it dries out, or as it is washed through by water penetrating the pavement structure. An open-textured sub-base provides lots of voids, gaps and gaping holes into which laying course material can be lost when the pavement is finally consolidated.
Extending the concern over the condition of the sub-base, in some critical applications a permeable geotextile will be used to cover the sub-base and so prevent any loss or 'trickle-down' of laying course material. The presence of such a membrane is likely to slightly reduce the degree of compaction recorded for any given depth of laying course material.
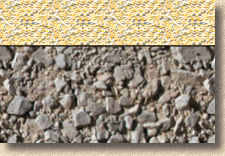
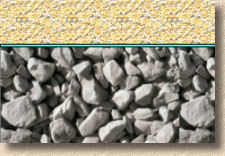
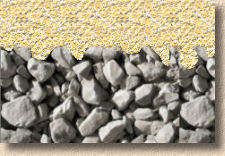
Equipment variables:
Another 'obvious' factor - a heavier, more powerful vibrating plate will achieve a greater degree of compaction than would a lighter, less powerful model. To achieve structural stability and minimise the risk of any settlement, the sub-base should be 'compacted to refusal', which is a particular point at which no further compaction is possible. In theory, this may require, say, 8 passes of a heavy plate or 16 passes of a lighter plate. In actuality, when a lighter plate is used, it's unlikely to be used for the full 16 passes (if that's what is needed to achieve 'compaction to refusal'). So, when the laying course material is placed, the blocks laid, the fact that there ius still some 'give' in the sub-base, even though it might only be a millimetre or two, can affect the degree to which the whole pavement compacts, and therefore the depth of screed required.
Further, a heavier, more powerful plate will be better able to compact to refusal the whole pavement structure, not just the individual layers that make up the pavement.
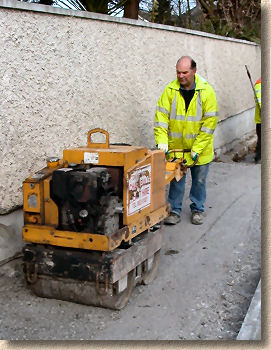
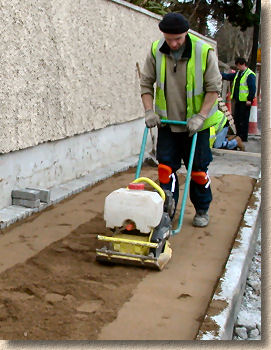
How do we manage?
All of these variables combine to a greater or lesser degree to affect just what amount of compaction can be achieved with any given sand (or other laying course material) on any given site, over any given sub-base (or base), using any given pavers and any given plate compactor.
The only way to accurately determine what screed depth is required on any particular project is trial and error. Just because, say, a screed depth of 43mm works perfectly on one project does not mean that it would give satisfactory results on a neighbouring job, or on a project in another part of the country, or with a different type of paver, or with a different type of bedding sand.
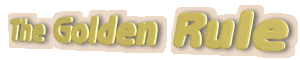

There is no hard and fast rule
for screed depth





Establishing screed depth - see table opposite
Table 1 opposite assumes a laying course thickness (ie: depth of sand) of between 40 mm and 50mm. As already noted, different laying course materials can give different results.
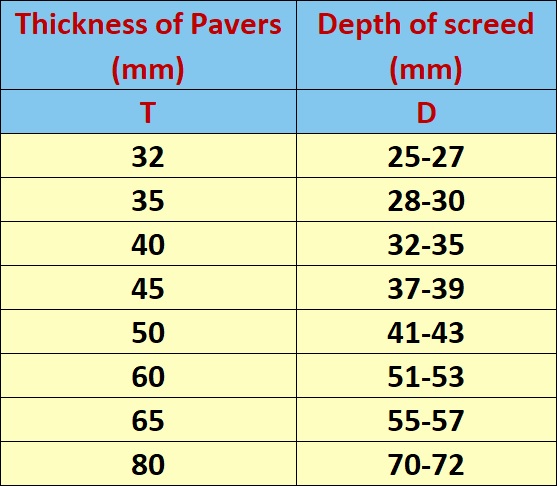
The information given in Table 1 is a rough guide to the typical sort of depths that generally work most of the time. However, it's impossible to say that these values are correct for each and every project - all those variables mentioned above come into play and can make the values stated in Table 1 inaccurate by as much as ± 5mm.
Trial and error is the only way to be sure that the screed depth established on a particular project will be satisfactory. A small-ish area (say a square metre or two) should be screeded using the mid-range value given in Table 1 for the depth of paver being laid. This test area should then be compacted to refusal (it will be necessary to ensure all edges are fully restrained, of course!) to determine whether the screed depth is too much, too little, or just right.
When pavers are left proud, then screed depth needs to increased: if the pavers are too low, then, obviously, the screed depth needs to be reduced. There's no need to be too precious about this as pavement can accommodate a bit of variation. So, if the pavers are found to be, say, 3mm high following consolidation, this could be accepted as satisfactory, as it's within the standard tolerance and unlikely to cause a problem. However, whenever pavers are found to be low, the screed depth must be lifted - pavers must never be left low, as this will allow surface water to collect. 3mm high is no problem, but 3mm low could result in a shallow 'bird bath' puddle, and shallow puddle never, ever repair themselves: they only ever accelerate the deterioration of the pavement.