Uses and Applications:
Far more widely used in Europe and North America than it is in Britain and Ireland, the cost-saving capability of Machine Laying is helping make it ever more attractive to developers and specifiers.
Over the past decades, modular flexible block paving has more than proved its worth as a pavement surface. It's relatively cheap, exceptionally reliable, aesthetically pleasing and simple to maintain and repair. So, if it's so good, why are we still laying blacktop ?
Well, one of the limitations of all modular paving is that it's less than ideal for vehicles travelling at speed, so until we shift exclusively to rail travel or develop levitating vehicles, it looks as though blacktop will be with us a while longer.
But that doesn't explain why blocks are not being used more widely for low speed areas, such as car parks. The answer to that conundrum lies in the speed of laying. On a good day, a three-man gang might lay 120 square metres. Two such gangs might manage 250 m² but maintaining such levels of productivity is hard work. Men tire, knees buckle, backs ache and wrists turn tender. Meanwhile, a six-man gang with a macadam paver machine could easily lay 1,800-2,000m² per shift, and be capable of repeating that feat day after day with little physical attrition.
If only we had a machine that could lay block paving!
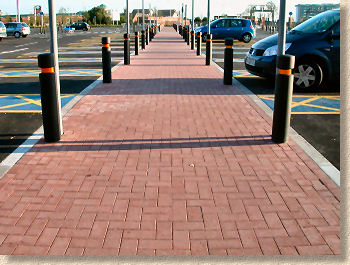
While several university teams are currently working on robotic block layers , and automated block laying machines for simple, straight runs are being used in Europe, the most reliable and practical method we have at the moment is the machine-aided cluster-laying system . This system relies on two key factors:
- The blocks have to be pre-arranged into clusters or panels that fit together to create a fully interlocked pavement
- The clusters have to be capable of being lifted, transported and placed mechanically, without blocks falling from the cluster during the process
Though these may seem minor problems, they have taken many years and large amounts of money to resolve, and the state of the industry is such that it is still developing and improving the techniques that have been put together to date. Just finding a way of arranging the blocks into a laying pattern cluster at the end of the manufacturing process has been an enormous challenge that has pushed process engineers and tooling manufacturers to new heights.
Definitions:
Block manufacturers such as Brett Paving now have reliable production lines that can assemble blocks into clusters, and then stack the clusters as layers to form a bale or pack for delivery to site. Once on site, a lifting head or 'clamp' attached to a lightweight highly manoeuvrable mobile crane could take one cluster-layer at a time and place it onto a prepared screeded laying course.
However, life's never that simple. Different sizes and shapes of blocks, different laying patterns all contribute to the resulting clusters having very different dimensions. If all we wanted to lay was 200x100mm blocks in a herringbone pattern, then just one lifting head would be required to grab, carry and place each cluster, regardless of which manufacturers supplied the blocks. But going back to the advantages of block paving mentioned at the beginning of this section, aesthetics are a major contributor to the appeal of CBPs, and so designers want variation and manufacturers want to be able to offer unique products, block formats not available from their competitors. And so the situation is that each unique block format/pattern combination requires a unique lifting head.
The answer? More process engineering and specialist fabrication!
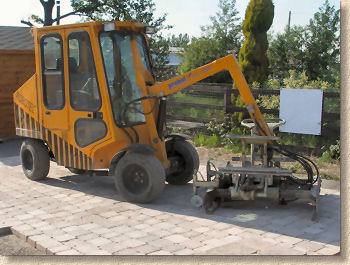
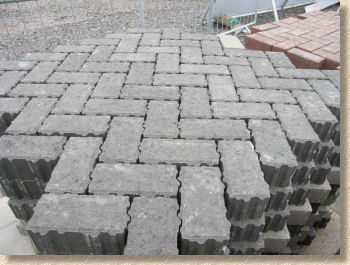
The essential components of a machine lay (ML) block paving system:
- - Blocks pre-arranged into interlocking clusters at factory
- - Custom lifting head to grab each cluster layer
- - Mobile lightweight crane to lift, carry and accurately place clusters
- - Machinery to spread, level and partially compact laying course
Sub-base and preparation:
Most ML paving contractors undertake only the paving. The sub-layer construction, drainage , kerbing and all other aspects of the pavement construction will often be undertaken by a separate civil engineering or groundwork contractor. Their brief is to construct to sub-base level a pavement that is competent, accurate and ready to have the laying course and paving blocks placed by the paving contractor.
The tolerance, accuracy and competence of the prepared sub-base is often a source of much jovial banter between groundworker and paving contractor. In fact, sometimes it becomes so jovial that restraint is required!
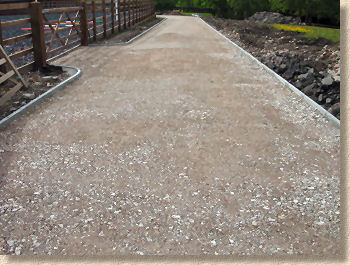
Laying course:
ML projects tend to be relatively large scale, often 1,000m² as a minimum, and so placing the laying course manually may not always be practical. That isn't to say that conventional laying course preparation and screeding techniques are never used: they are, but when the circumstances warrant it, mechanical placement/screeding of the laying course can be faster, cheaper and less labour intensive than conventional methods. After all, who wants to be hand-screeding a 10,000m² car park?
Manual preparation
On medium-scale projects, or where there are twists and turns, ironwork and other obstructions and impediments, conventional manual laying course screeding is most likely to be used.
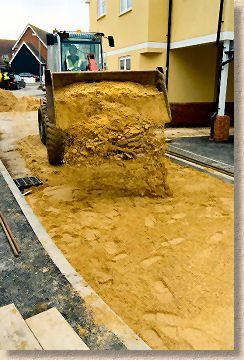
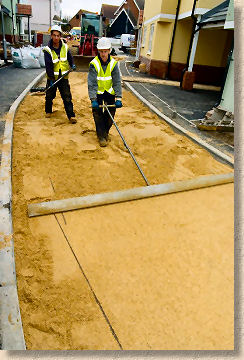
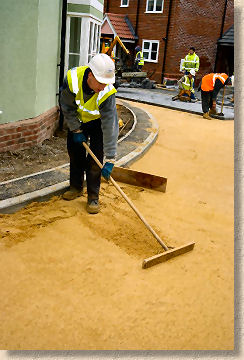
Mechanical preparation
Luckily, all those asphalt paver machines that are in danger of being made redundant by the upsurge of interest in ML-CBPs and the consequent reduction in demand for bituminous surfacing can find a new lease of life placing, screeding and partially compacting tens of thousands of square metres of laying course material, with minimal modification.
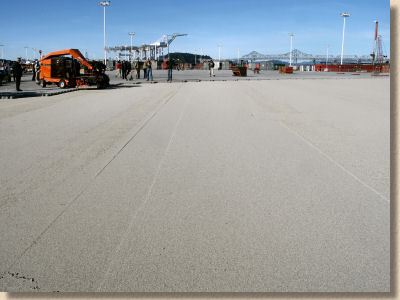
Other techniques favoured by different contractors include the use of vibrating beam screeds running over screed rails and the ever-popular dragging a machine-mounted heavy screed bar over screed rails, as shown below.
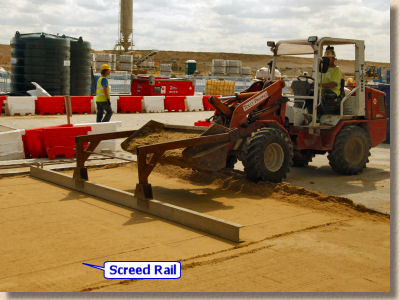
A loading shovel is used to drop and rough-out loose laying course material between screed rails with ample surcharge (technical talk meaning there's more loose aggregate than will be needed). The aggregate is then levelled and lightly compacted by having the loading shovel reverse out of the area, drawing the screed bar in its wake and so levelling the laying course material in a single pass (hopefully).
Laying Course Material
The material used for the laying course is exactly the same as would be used with manual laying although experience suggests more attention is paid to moisture content than is often the case on hand-laid projects. On conventional flexible construction , a grit or grit sand compatible with Table D2 would be used, while for permeable pavements ( CBPP ) a grit or fine aggregate as defined by Table D6 is what should be used.
In practice, placing the laying course is undertaken with one eye on the weather. There's no point spreading a thousand metres of laying course if the forecast predicts torrential rain, gale-force winds or several degrees of frost. In good weather, and when the scale of the job permits, laying course placement may be as much as 48 hours (2 working days) ahead of the leading edge but most ML contractors prefer to keep it to 4 hours or so to prevent scour or accidental disturbance to the carefully prepared laying course.
Placing Blocks:
This is the part of the process that is radically different to manual installations. A typical working gang will consist of three operatives: one to drive the laying machine, one to align the cluster/head, and a third to service the other two, whether it be bringing in new packs of blocks for the laying machine or providing replacement blocks for the occasional chipped/spalled/ugly block.
Remember, the whole point of machine lay installation is to reduce the number of operatives to a minimum. Gangs that rely on two, three or even more operatives working around the cluster are defeating the object!
To be fair to the laying gang shown in the video, the fact that they are laying non-closing clusters (explained below) does require some additional labour, but I'm not sure it warrants quite so many operatives swarming around!
Fresh packs of pre-arranged blocks are delivered close to the leading edge, reducing the travel time for the installation machine, but allowing sufficient room for manoeuvring. As with manual laying, randomisation of blocks is important, so it is common practice for the installation machine to take layers from three or more open packs, alternating each lift between the packs.
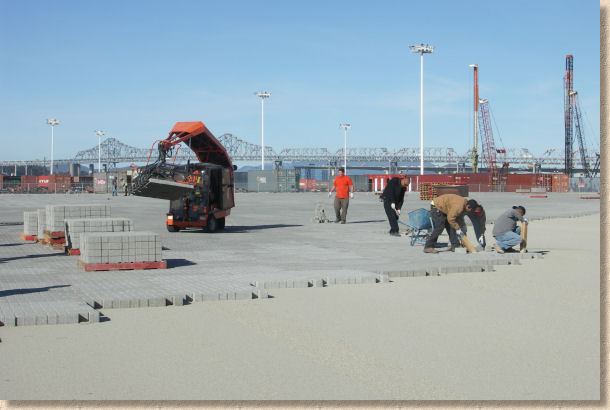
The lifting head is lowered over the top layer of blocks which is then grabbed by the hydraulic clamps which also serve to tighten-up the layer and so correct any minor misalignment or disturbance that might have happened to the blocks since the pack left the factory.
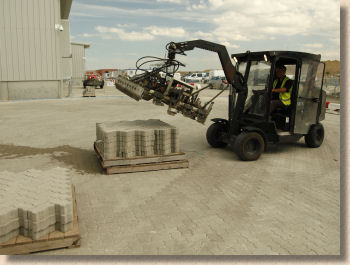
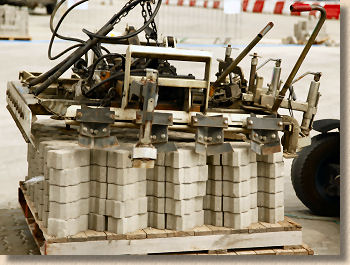
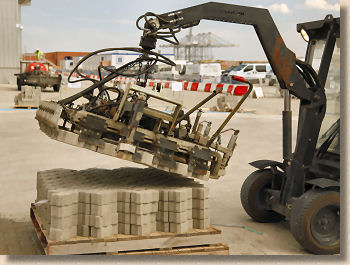
The pressure applied by the side clamps is sufficient to hold the whole layer of blocks in place, although the occasional block may come loose during transit and will need to be manually fitted into the cluster once it is laid.
The laying machine manoeuvres itself into position to place the cluster in the correct position. The second operative will use the handles fitted to the lifting head to guide the cluster into position, aligning the new blocks tight against those laid previously, and then giving the signal for the driver to release the clamps and so set the blocks onto the bed.
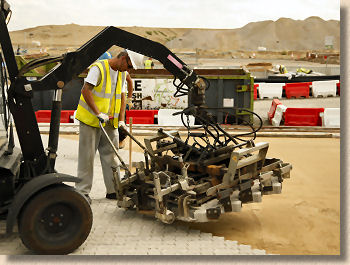
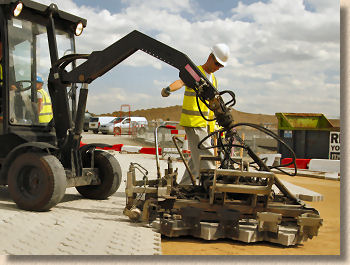
The laying machine reverses away from the laying face and moves to collect the next cluster while the block-hand manually corrects any misalignment and uses a block hammer to ensure the newly placed blocks are tight against those laid previously.
The whole cycle should take somewhere around 10-15 seconds, giving a laying rate of around 5m² per minute, which allowing for the usual site hassles and interruptions, should average around 100m² per hour on an open site. It's not unusual for experienced and highly-motivated (ie: well paid) gangs to lay in excess of 1,000m² in a single shift.
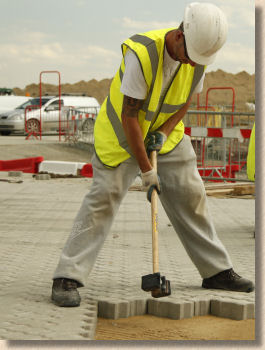
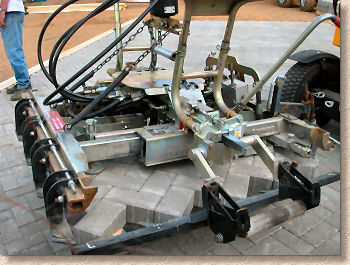
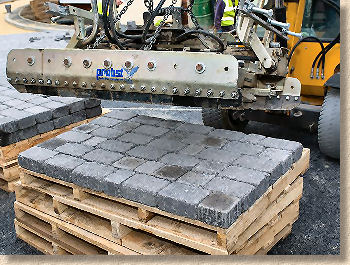
Compliance Checks and Cutting:
One of the functions of the third gang member is to check the paving as it is laid, ensuring alignment is accurate, that any damaged or broken blocks are replaced with good units, and that there are no significant deviations from level. This is known as compliance checking.
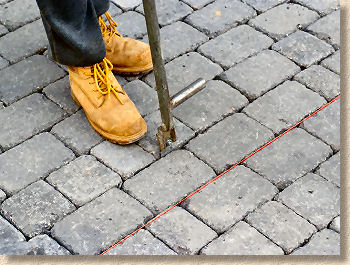
Most large scale machine-laid jobs involve proportionally far less cutting-in than would occur on a typical driveway project. Consider a 5 x 10m driveway: 50m² and 30m of cutting (5 + 10 + 5 + 10) is equivalent to 0.6m of cuts per square metre. In contrast, a 30 x 30m freight yard contains 900m² and 120m of cuts (30 + 30 + 30 + 30), equivalent to 0.13m per square metre.
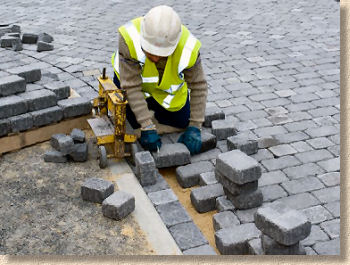
Regardless, cutting-in is undertaken in exactly the same way as would be the case for hand-laid paving, following the rules for inboard cutting. While some contractors prefer to use a cut-off saw, the problem of controlling the resultant dust is beginning to persuade more and more contractors to use splitters as a faster, cleaner and cheaper alternative.
Compaction:
For almost as long as we have been laying CBPs in Britain and Ireland, there has been arguments regarding whether jointing should be done before or after compaction. There are pros and cons to both strategies, which are examined more thoroughly elsewhere on this site , but for the vast majority of Machine Lay jobs, the blocks are compacted first, and then jointed.
So, once cutting-in and compliance checks are completed, compaction will begin, and given the scale of most Machine Lay projects, having a single vibrating plate compactor marched up and down the job would take a considerable amount of time, and so most contractors will use linked machines: two or three (or even more) heavy vibrating plate compactors lashed together, multiplying the area covered by each pass but still controlled by a single operative.
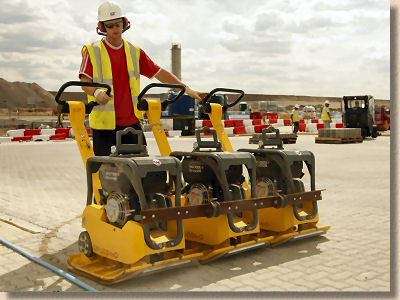
Jointing:
Compaction complete, the next step is jointing. This is, in principal, exactly the same procedure as would be used on smaller, hand-laid installations, where a suitable fine aggregate (usually kiln dried sand in Britain and Ireland) is scattered across the entire surface and then brushed in to the open joints.
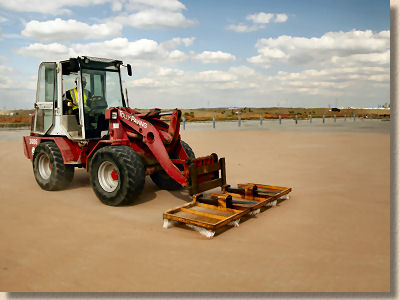
However, given the scale of these machine laid projects, having some poor sod endlessly traipsing up and down the site leaning on a soft brush is not feasible, and so most contractors will rely on machine mounted sweepers to disperse the sand and encourage it into the joints.
Summary:
Machine Lay is popular in Europe, and is growing rapidly in North America, but is vastly underused in Britain and Ireland. For a decade or so when the economy was booming, it seemed that the bottleneck in the uptake of Machine Lay was the limited number of suitable contractors willing to invest in the plant, the training and the commitment needed, but it is becoming increasingly obvious that there is an inherent conservatism with designers and engineers who are reluctant or even unwilling to appreciate the significant benefits that can be achieved by using Machine Laid CBPs in place of other surfaces.
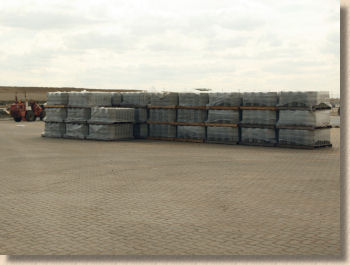
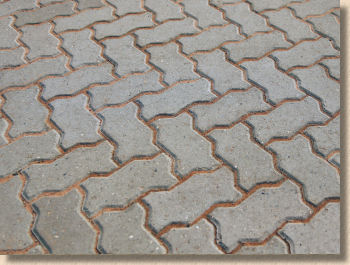
It is an incredibly simple and efficient system that is so fast it's verging on unbelievable. Blocks can be manufactured to incorporate a high percentage of recycled content and eco-friendlier cements, so helping meet sustainability targets for many projects. It also brings with it all the other advantages of a flexible, segmental pavement such as being cheap and easy to repair.
As the industry becomes more aware of the ergonomic costs of large hand-laid projects and moves to limit the use of manual labour in heavy, repetitive tasks, Machine Lay is the obvious answer. Hey! If they are doing it in Germany, you *know* it's going to be happenning here very soon!
Learn all about the possibilities of Machine Laid Concrete Block Paving with Brett Paving
- Omega - conventional rectangular blocks for machine lay
- Omega Flow - permeable and machine layable
- Antique Alpha - classic, aged look but laid by machine
- Grass Flow - For sensitive sites. Permeable and ML
- Zeta Lock - the heavy duty choice for ML paving blocks
Further Information:

Sileby Road
Barrow upon Soar
Leicestershire
LE12 8LX

Tel: 0845 6080 570